

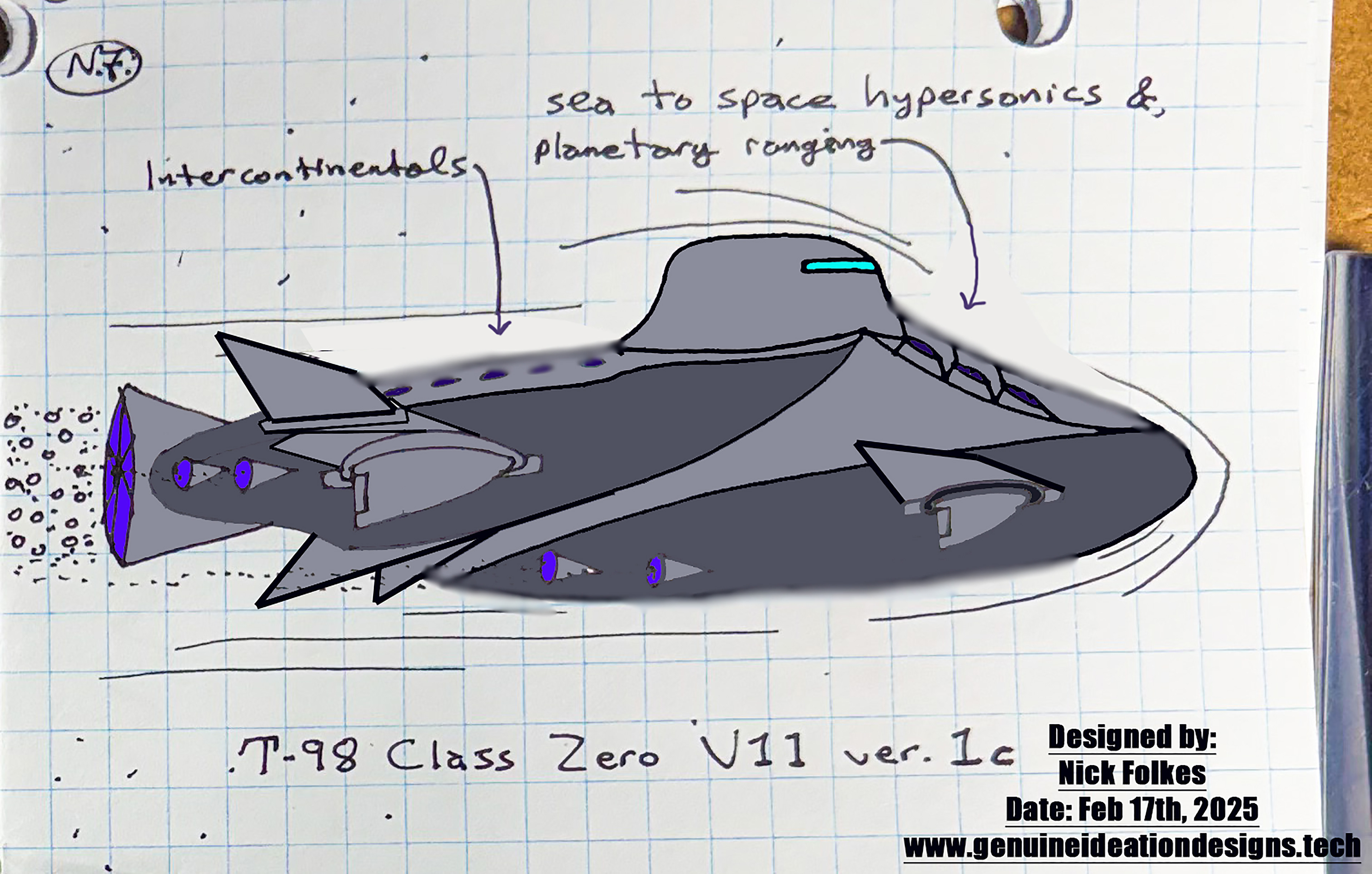
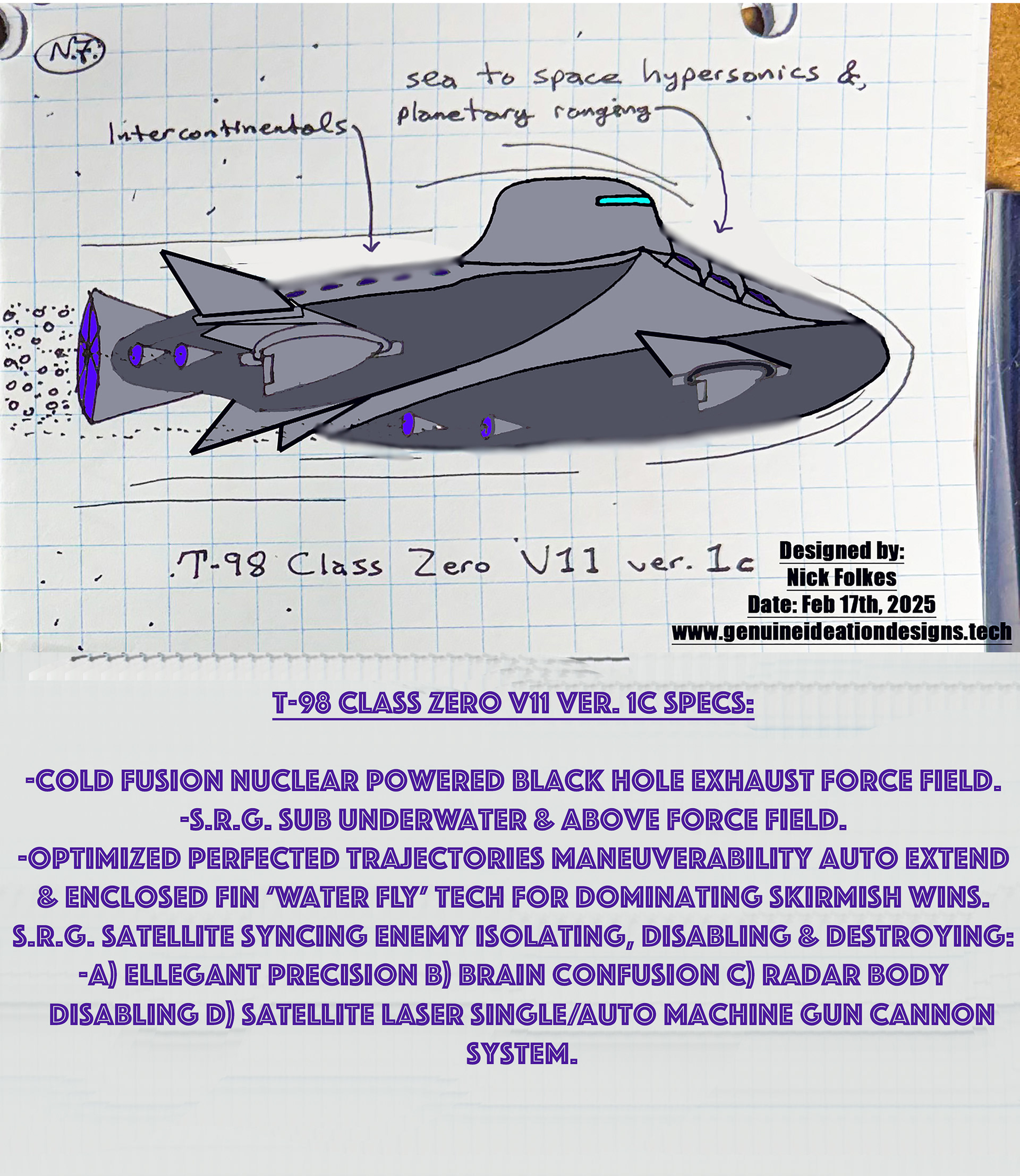
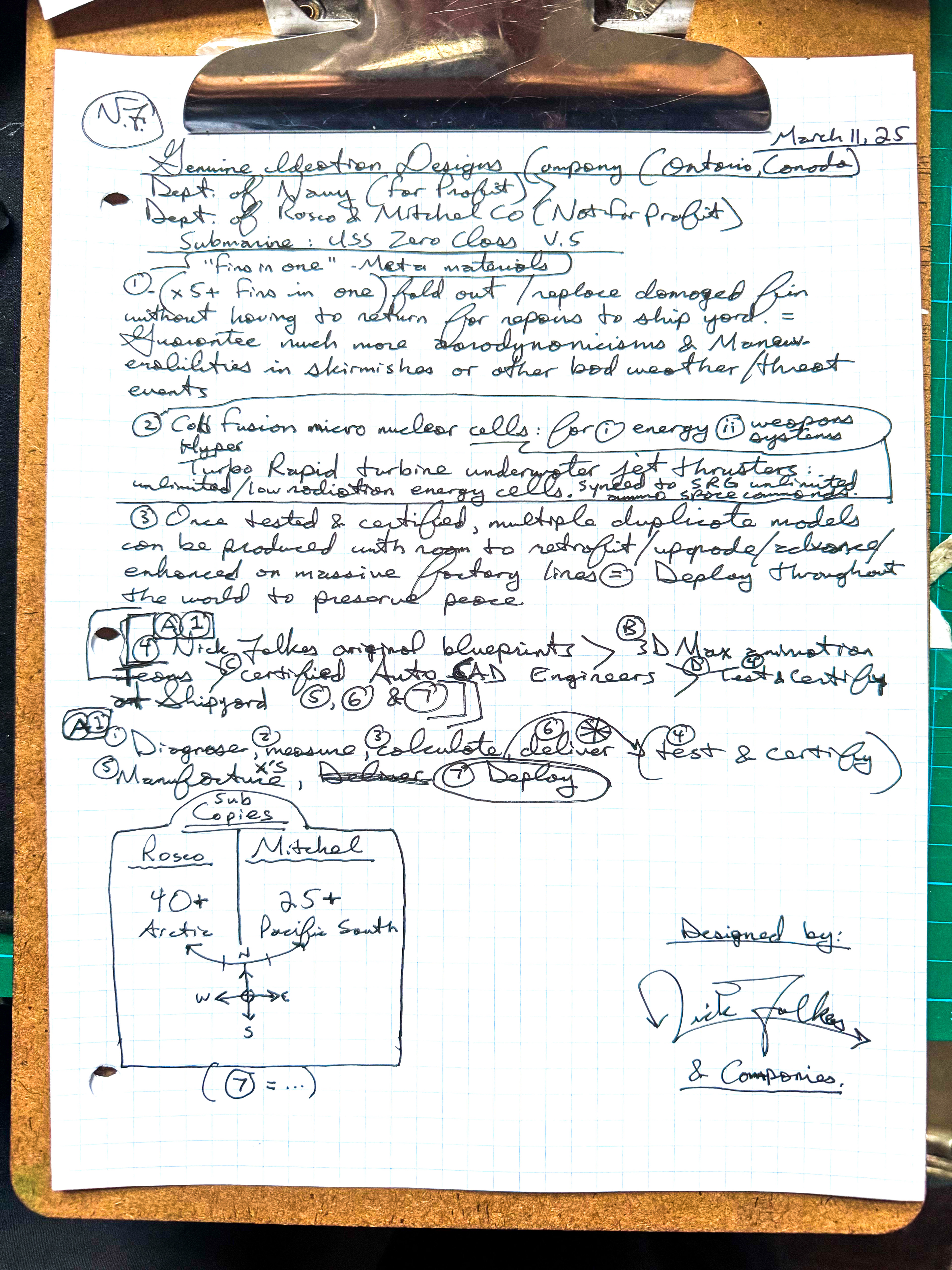
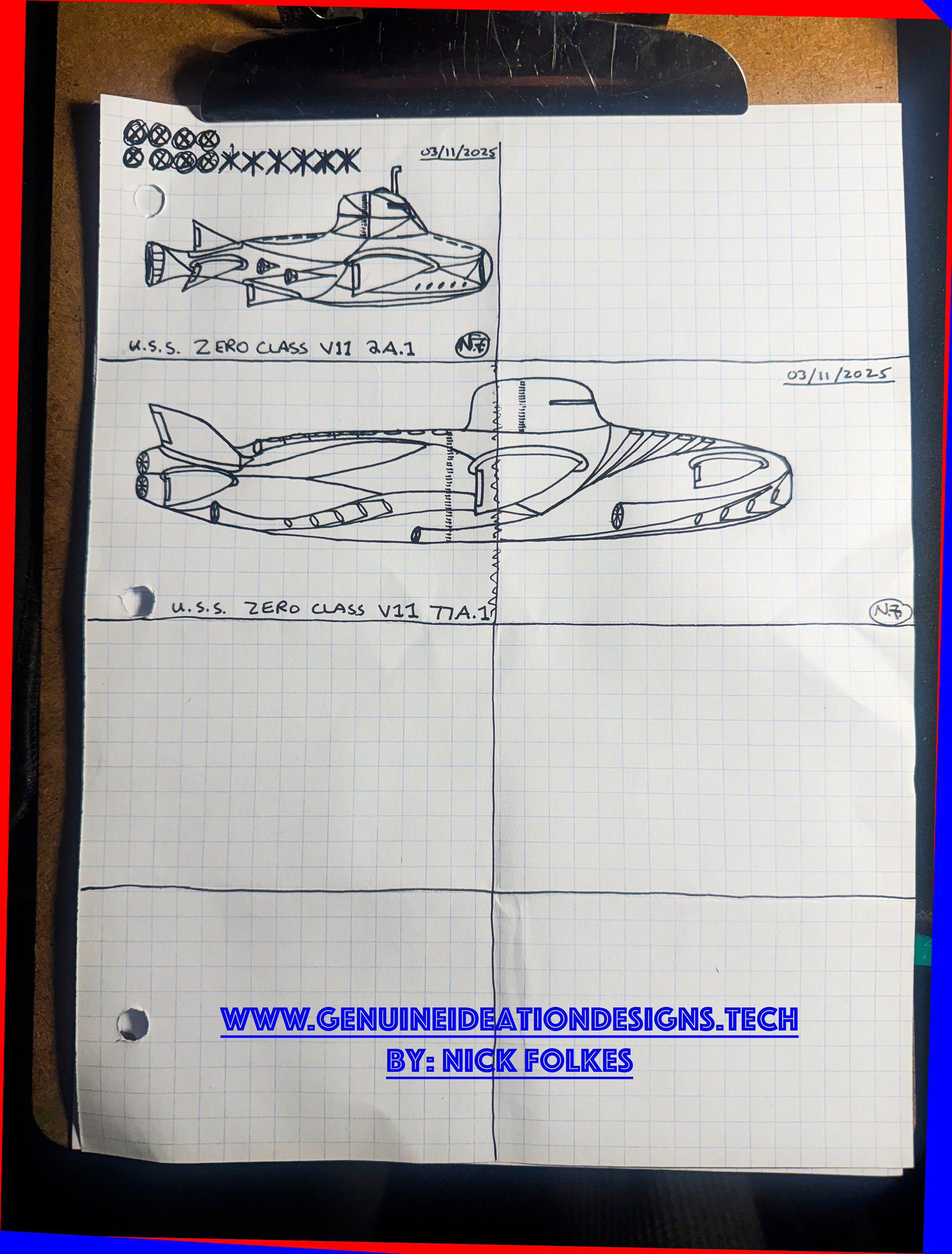
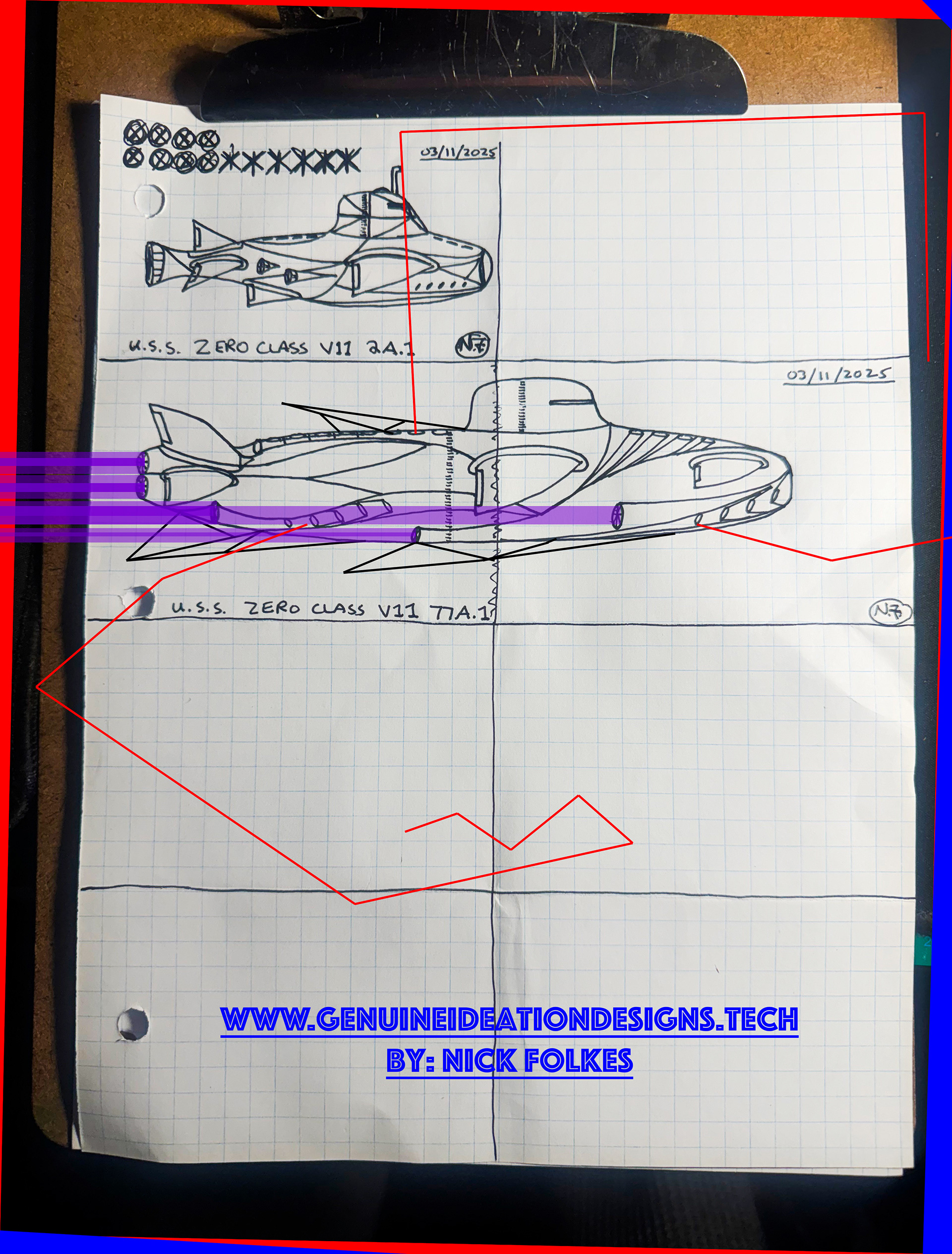
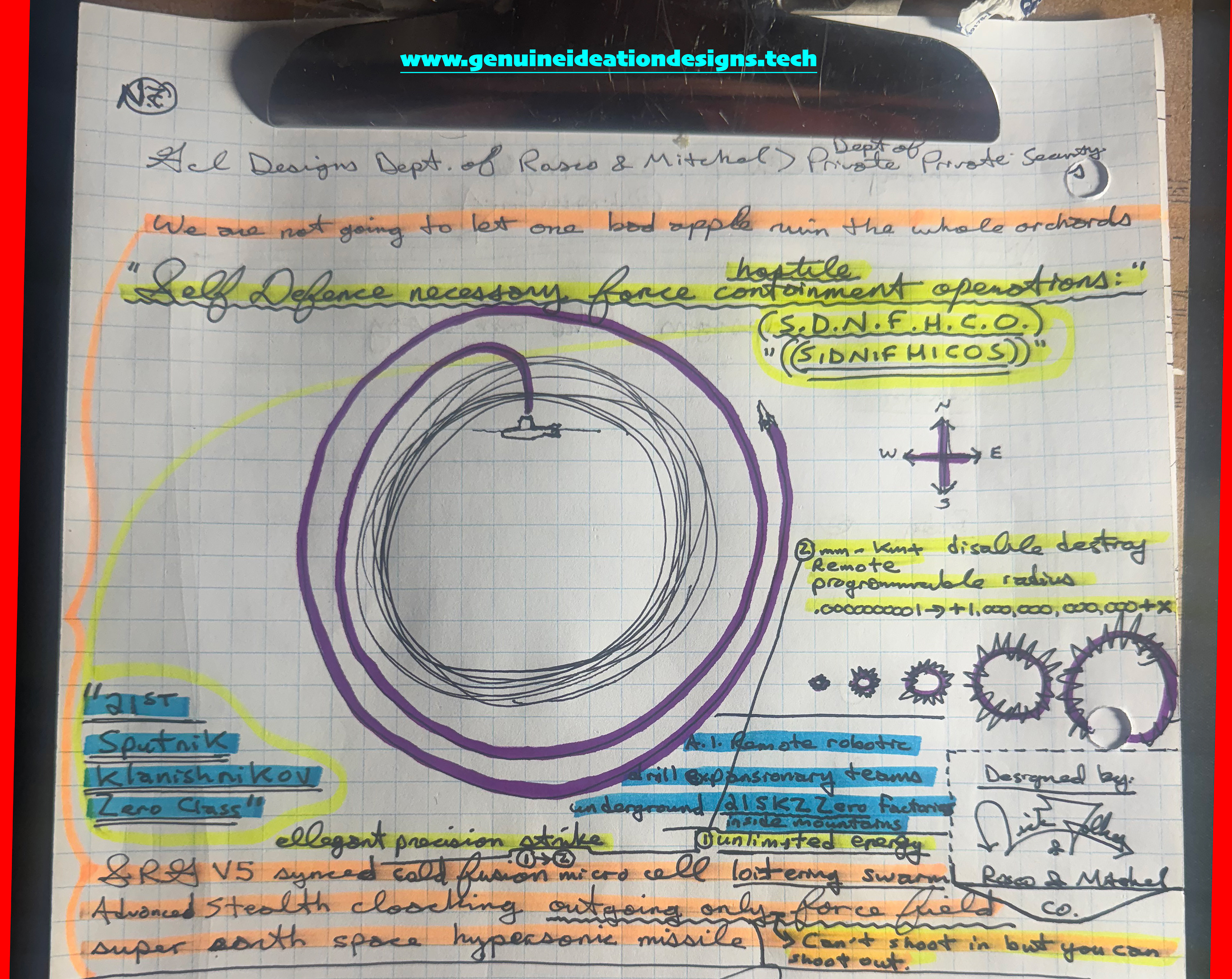
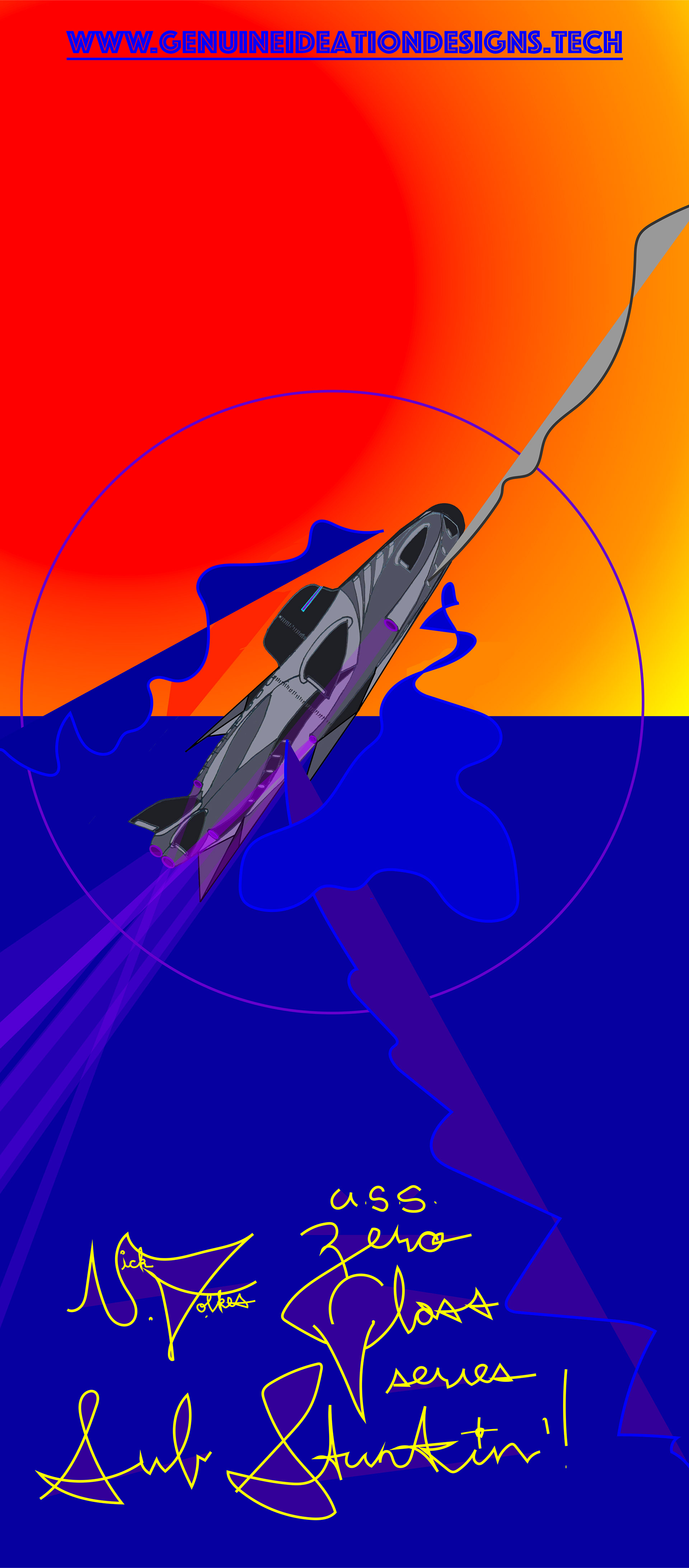
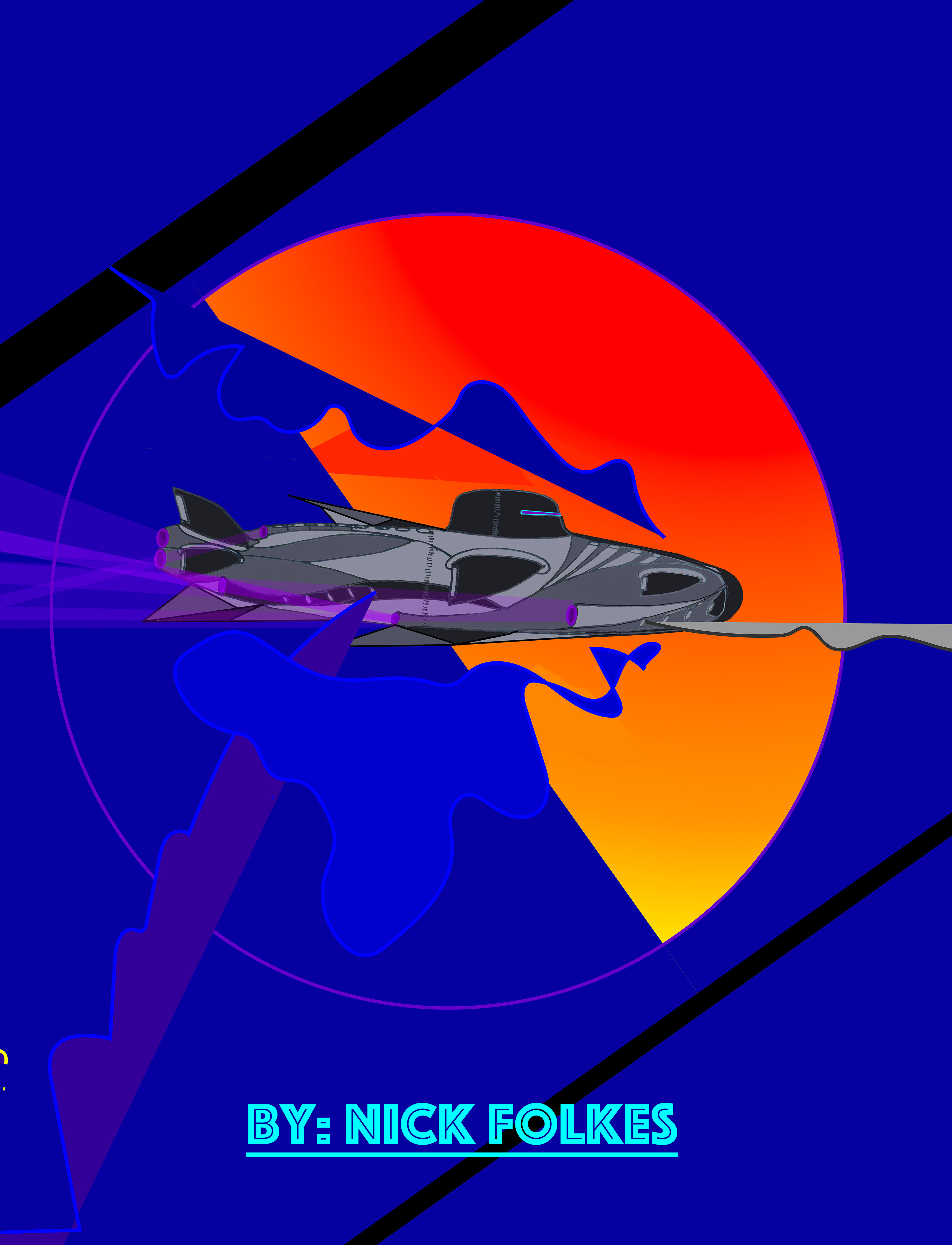
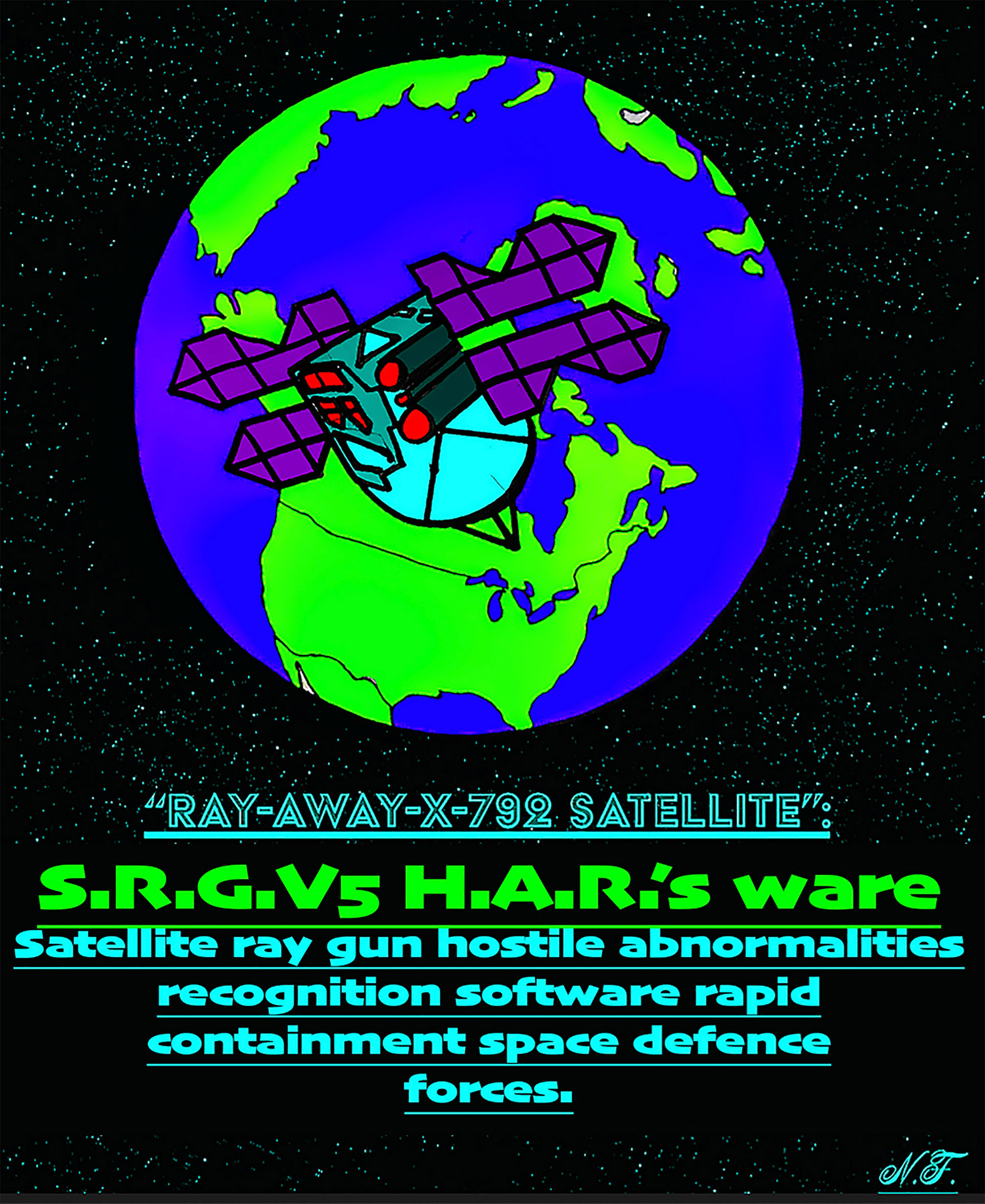
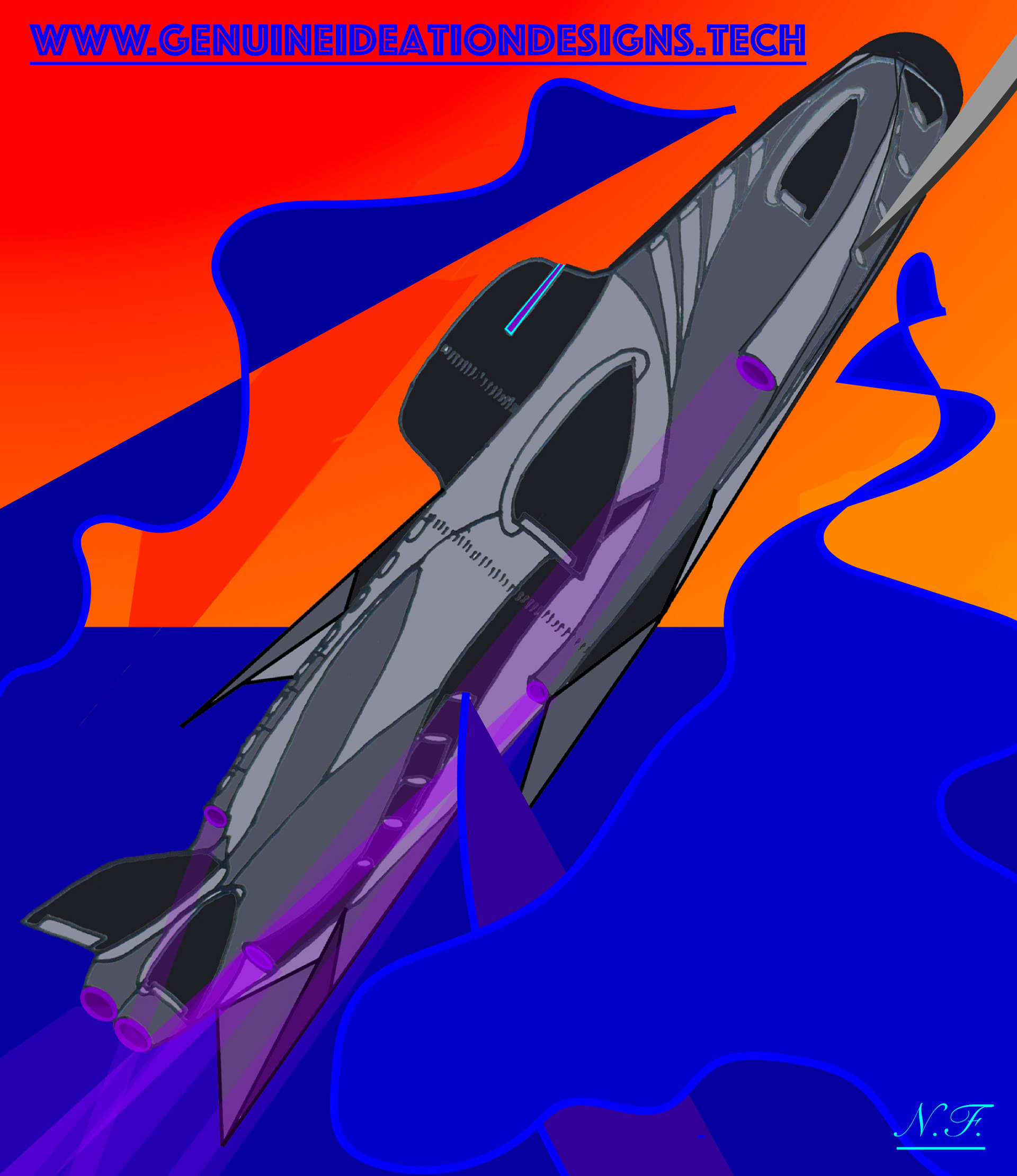
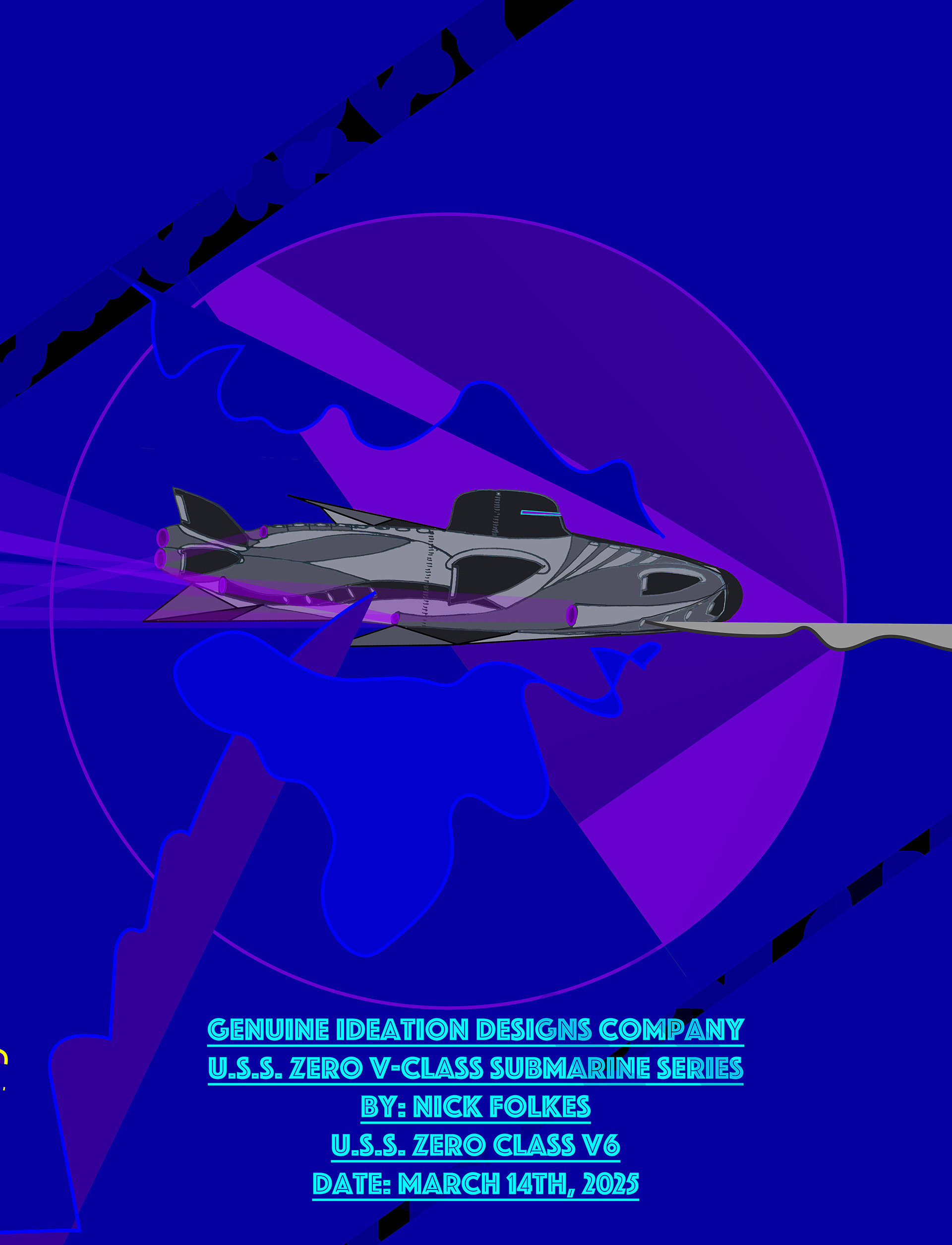
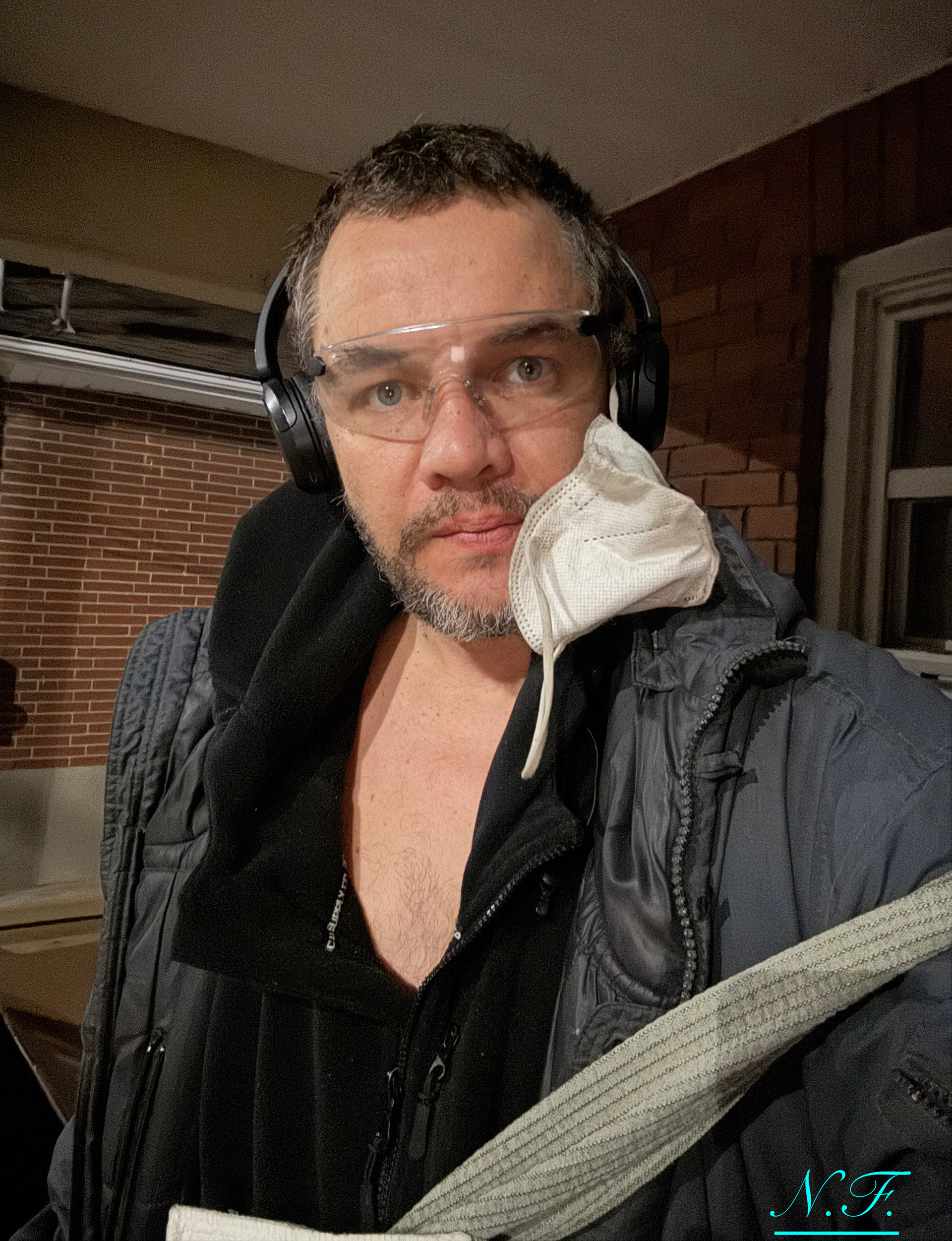
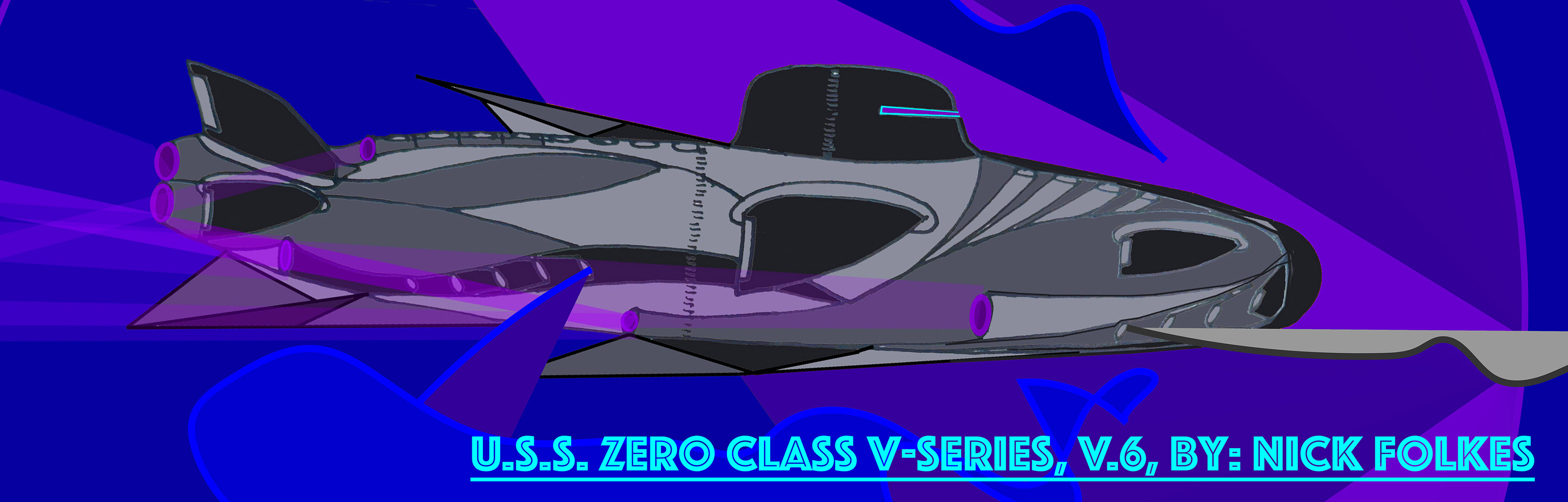
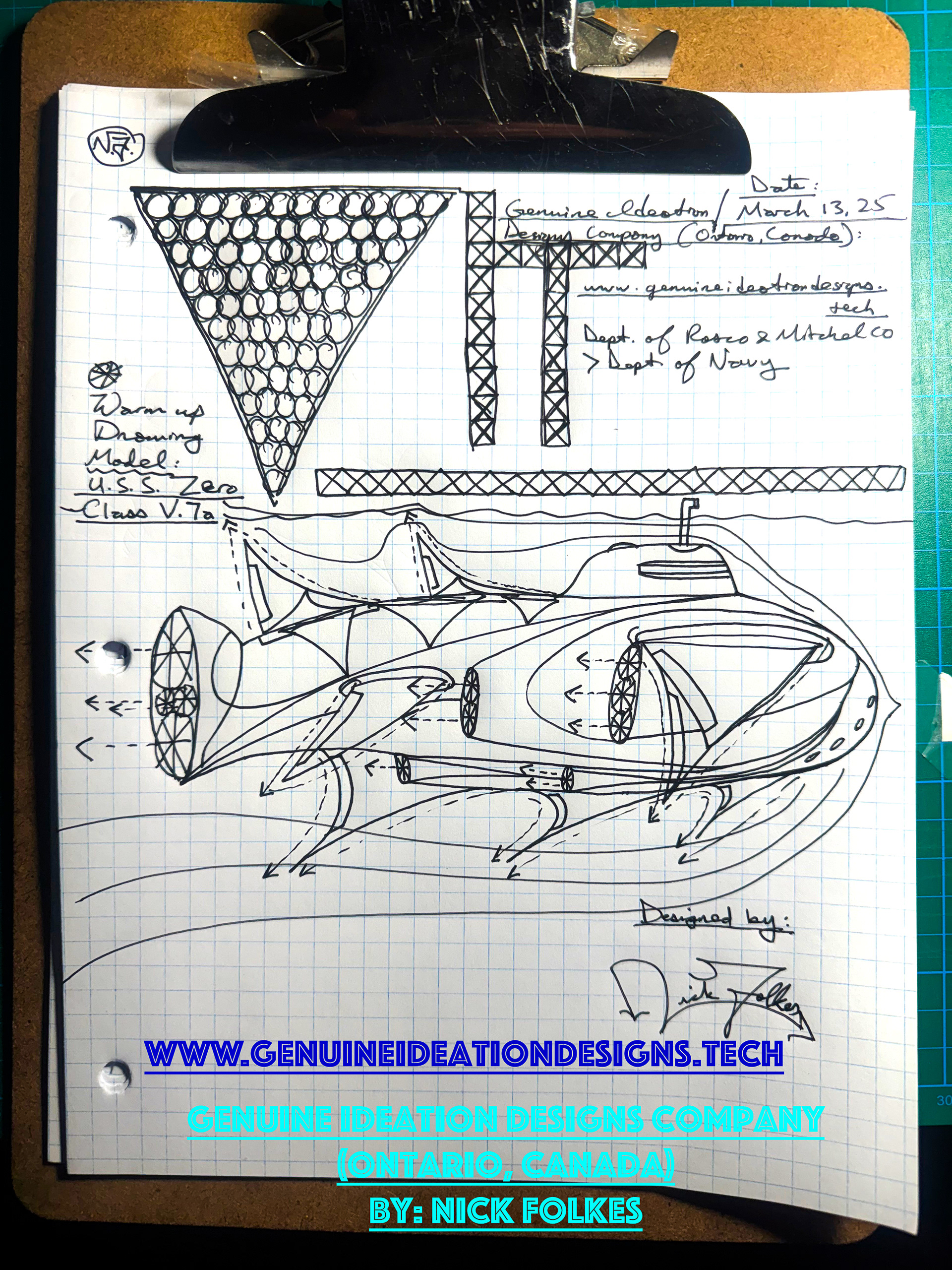
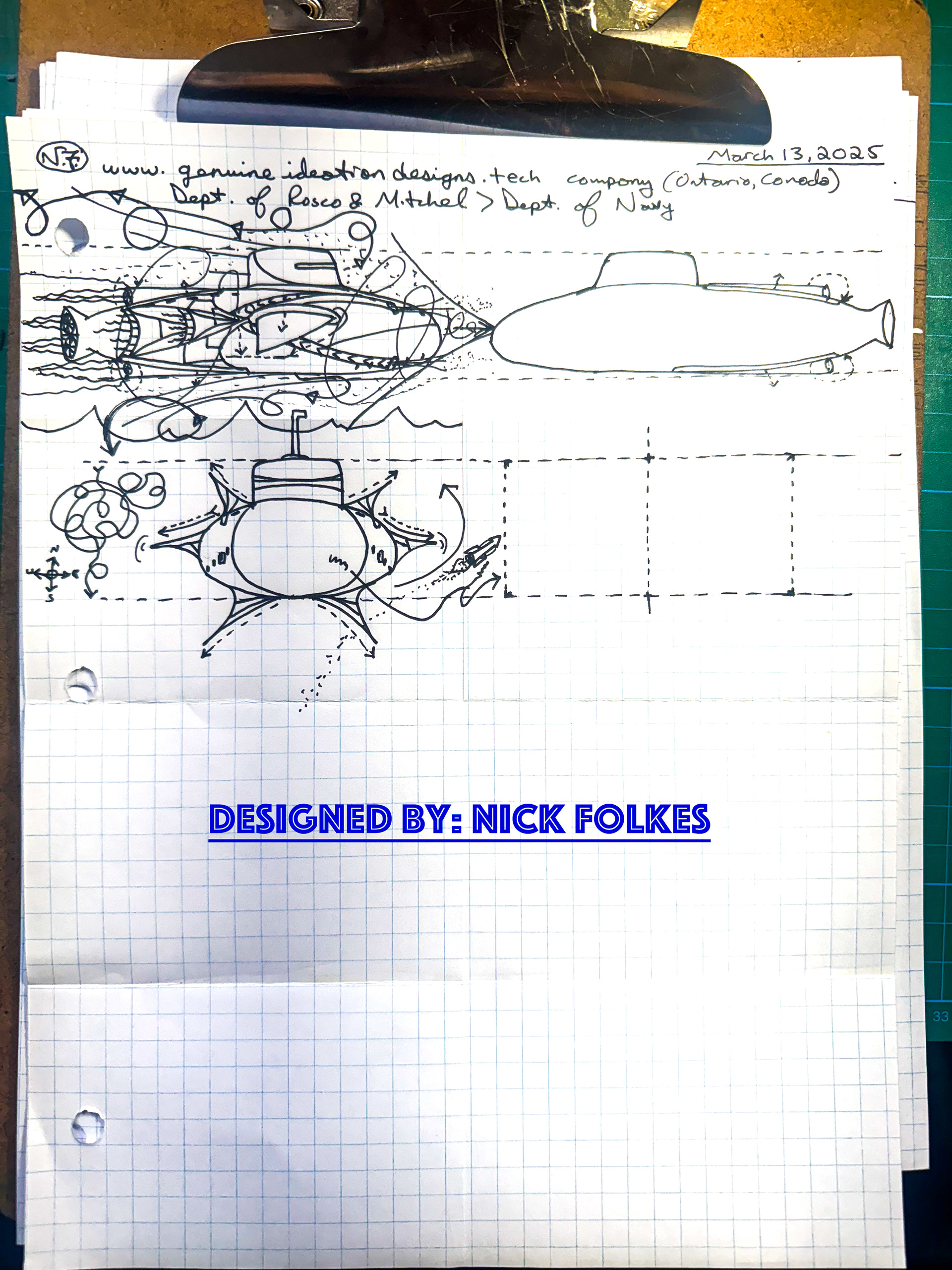
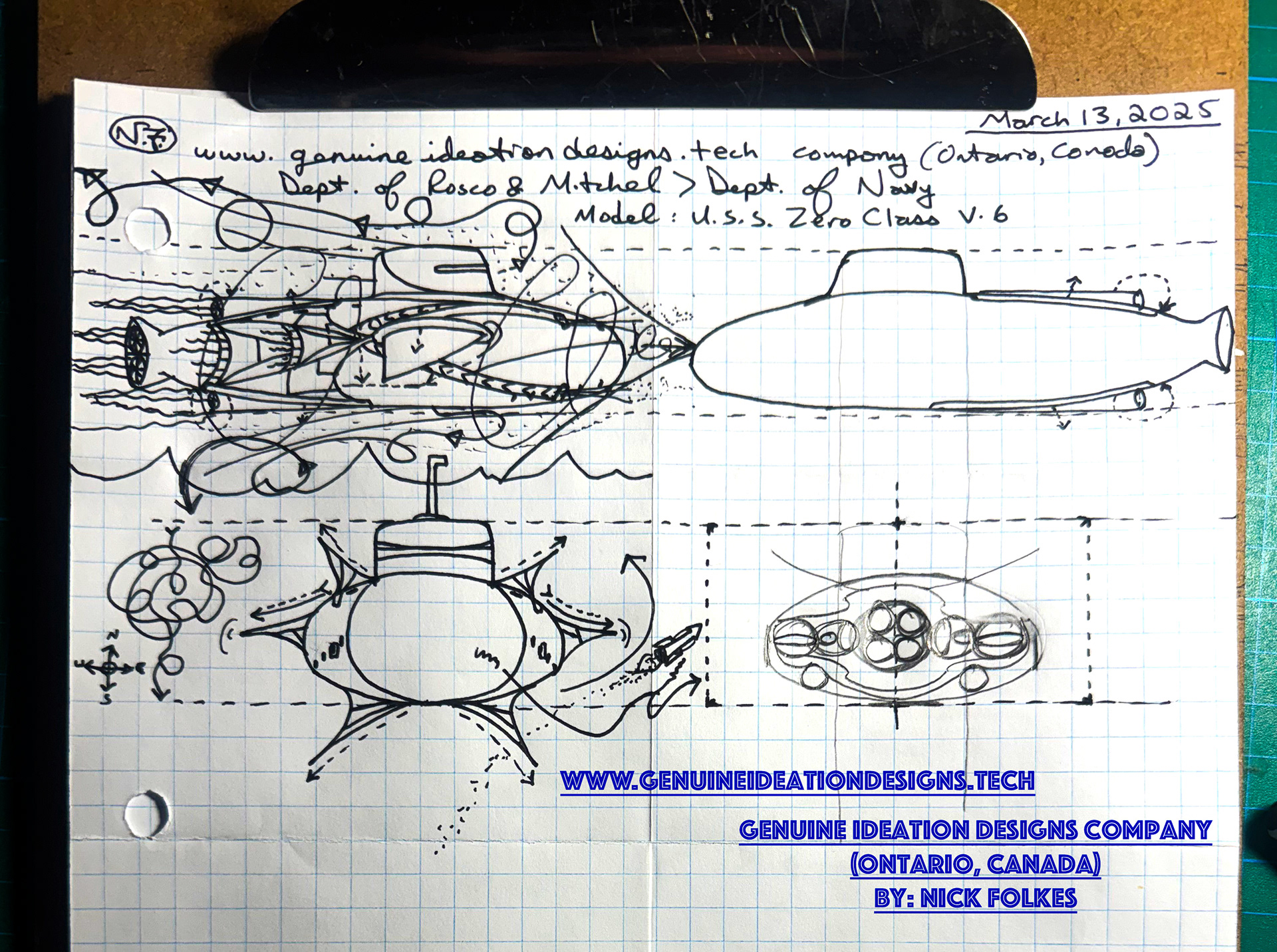
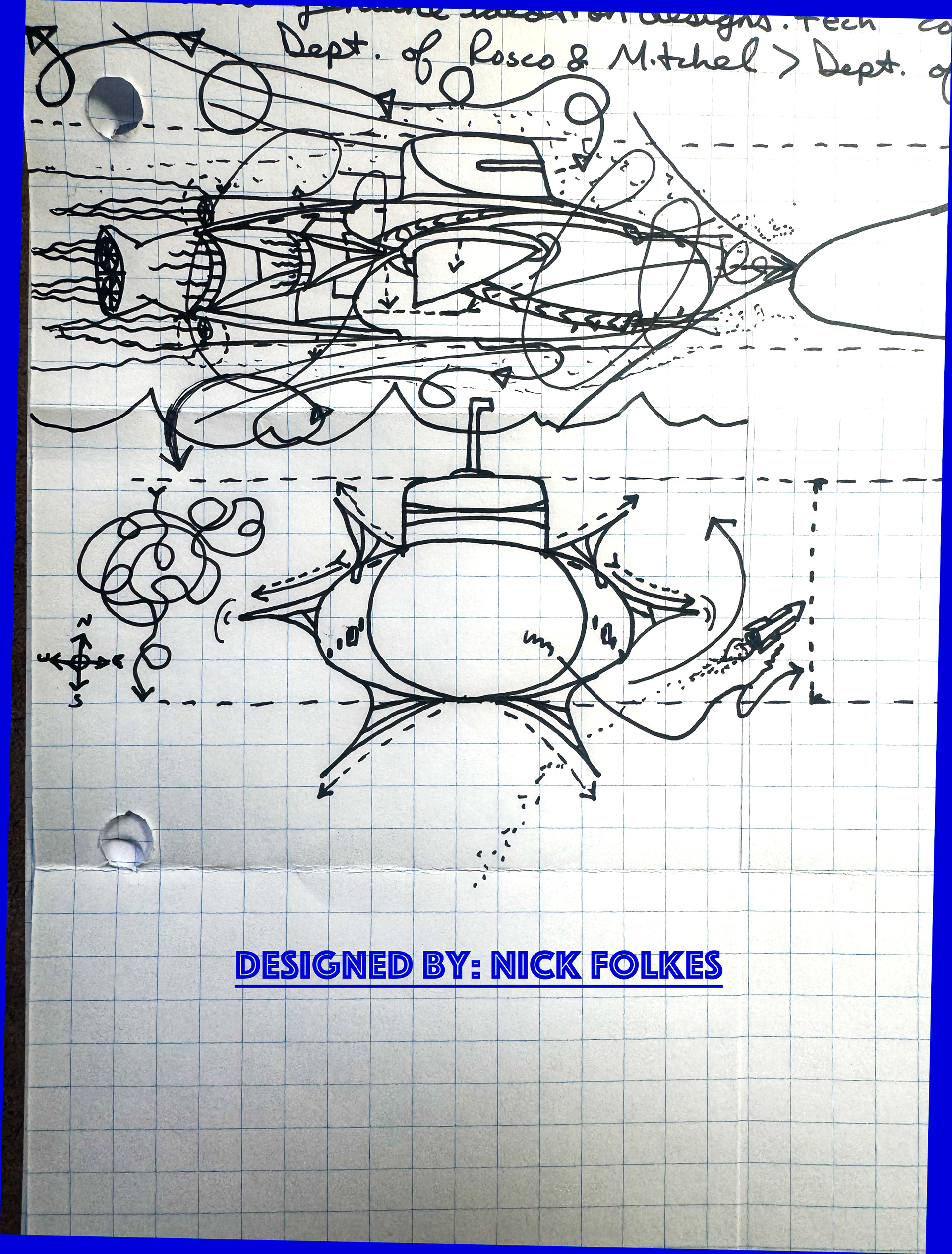
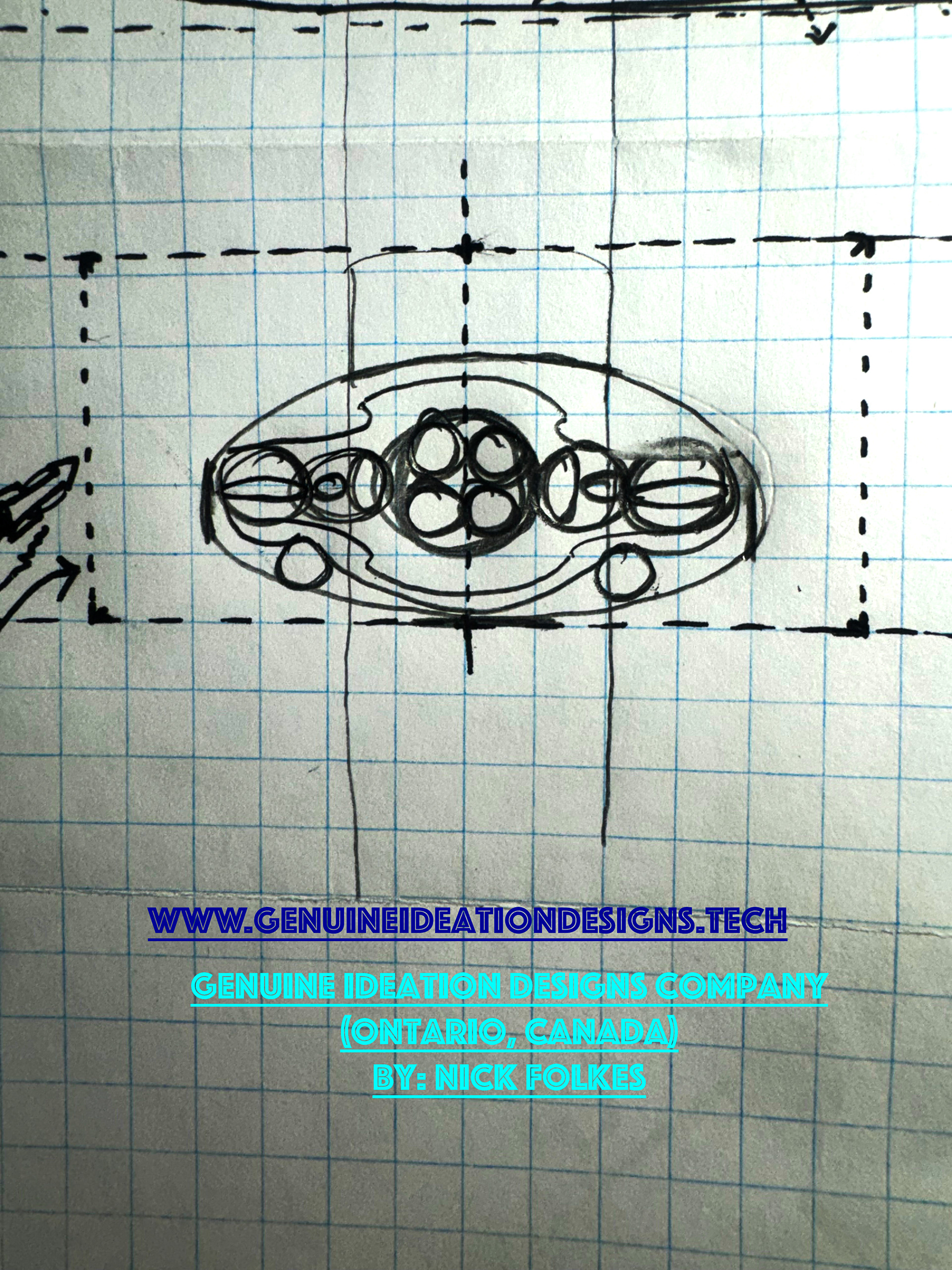
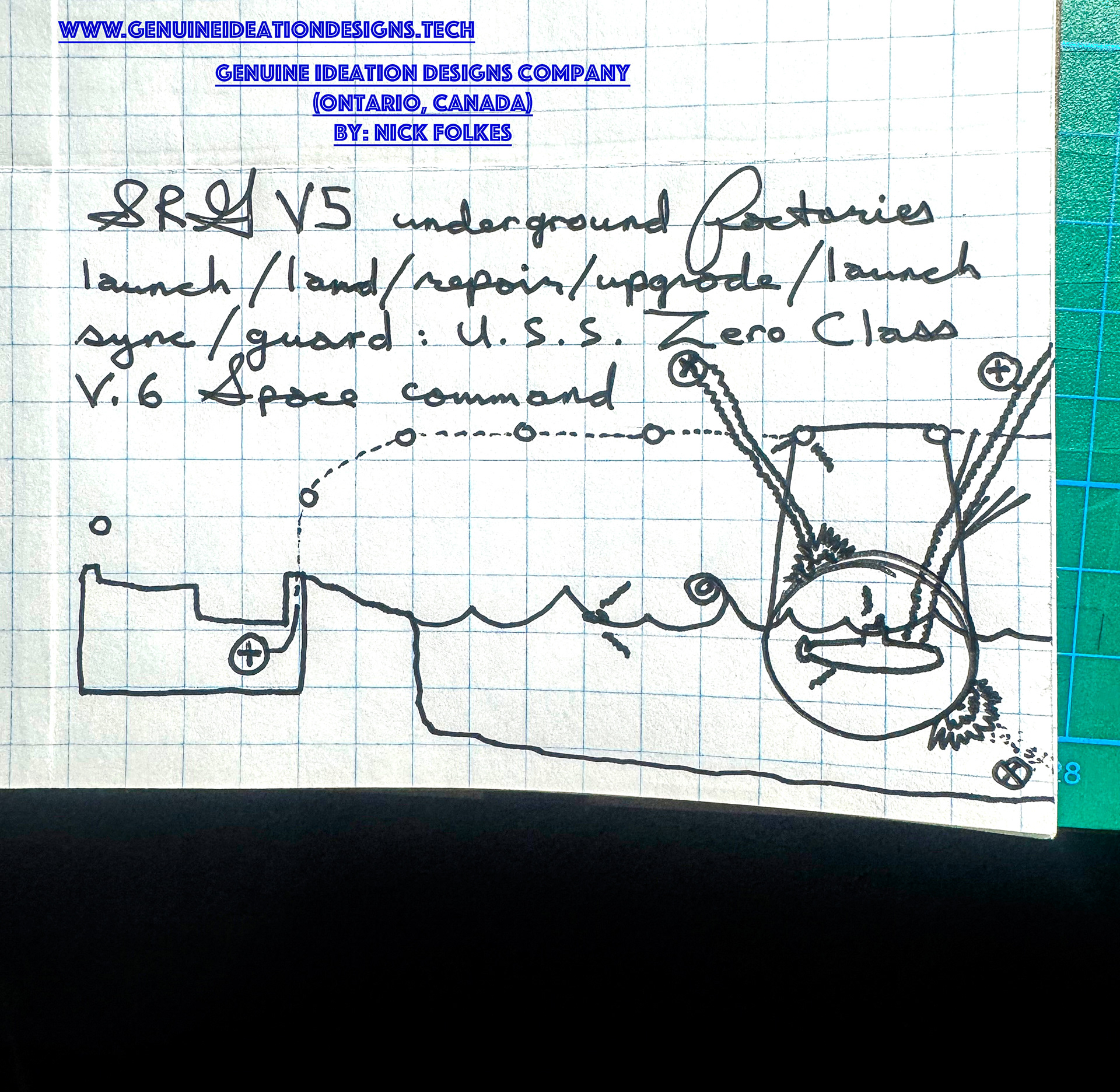
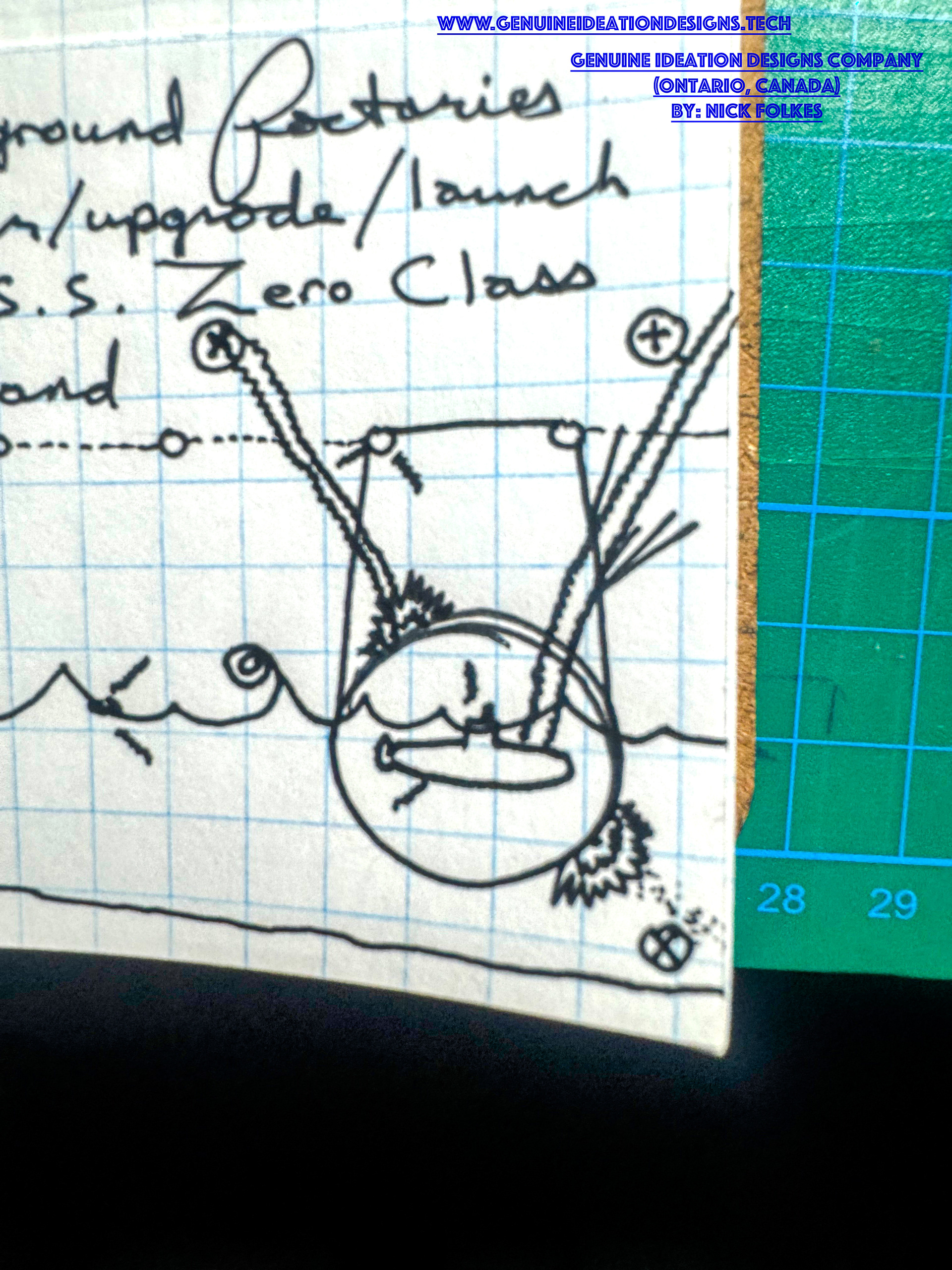
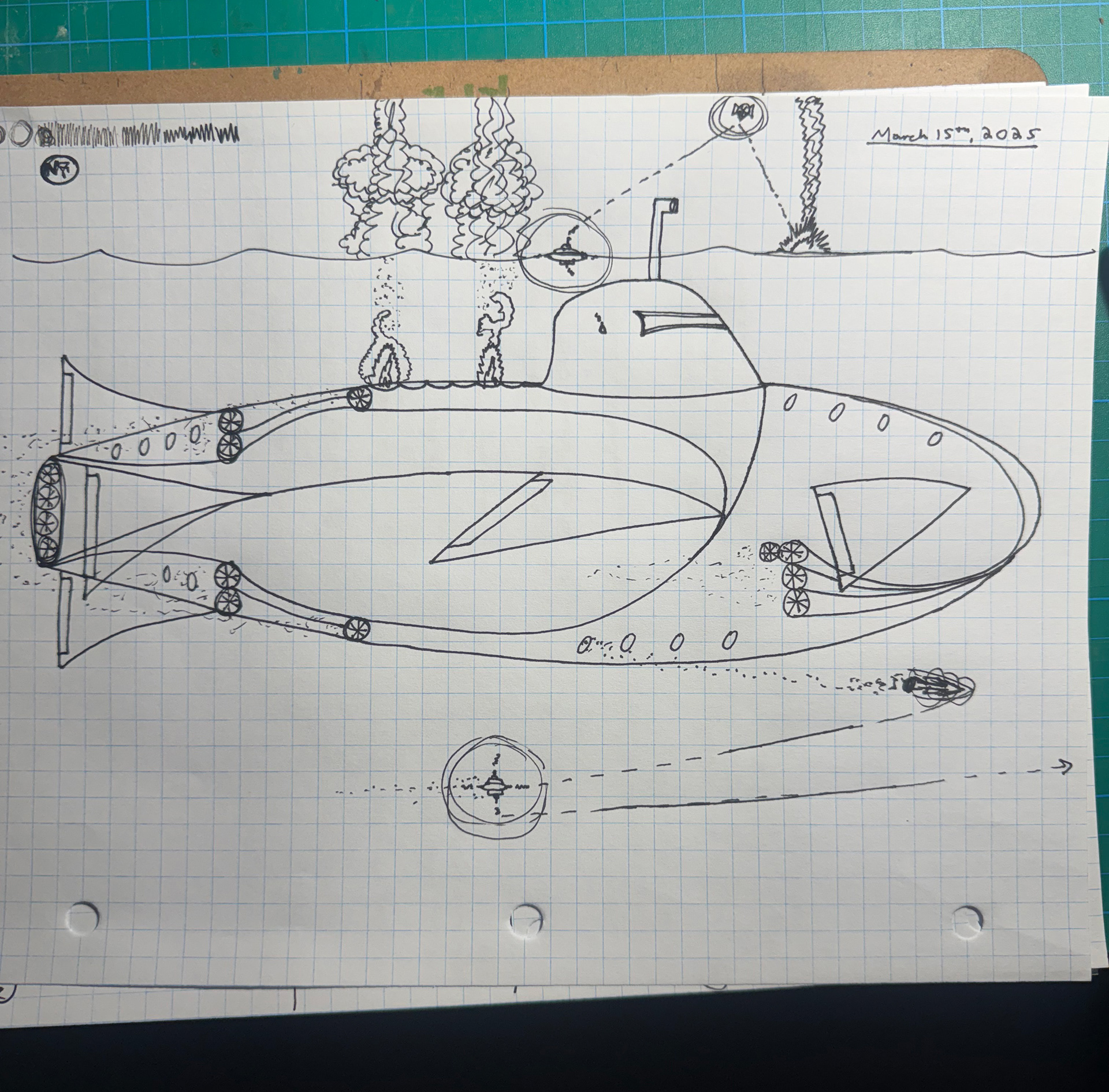
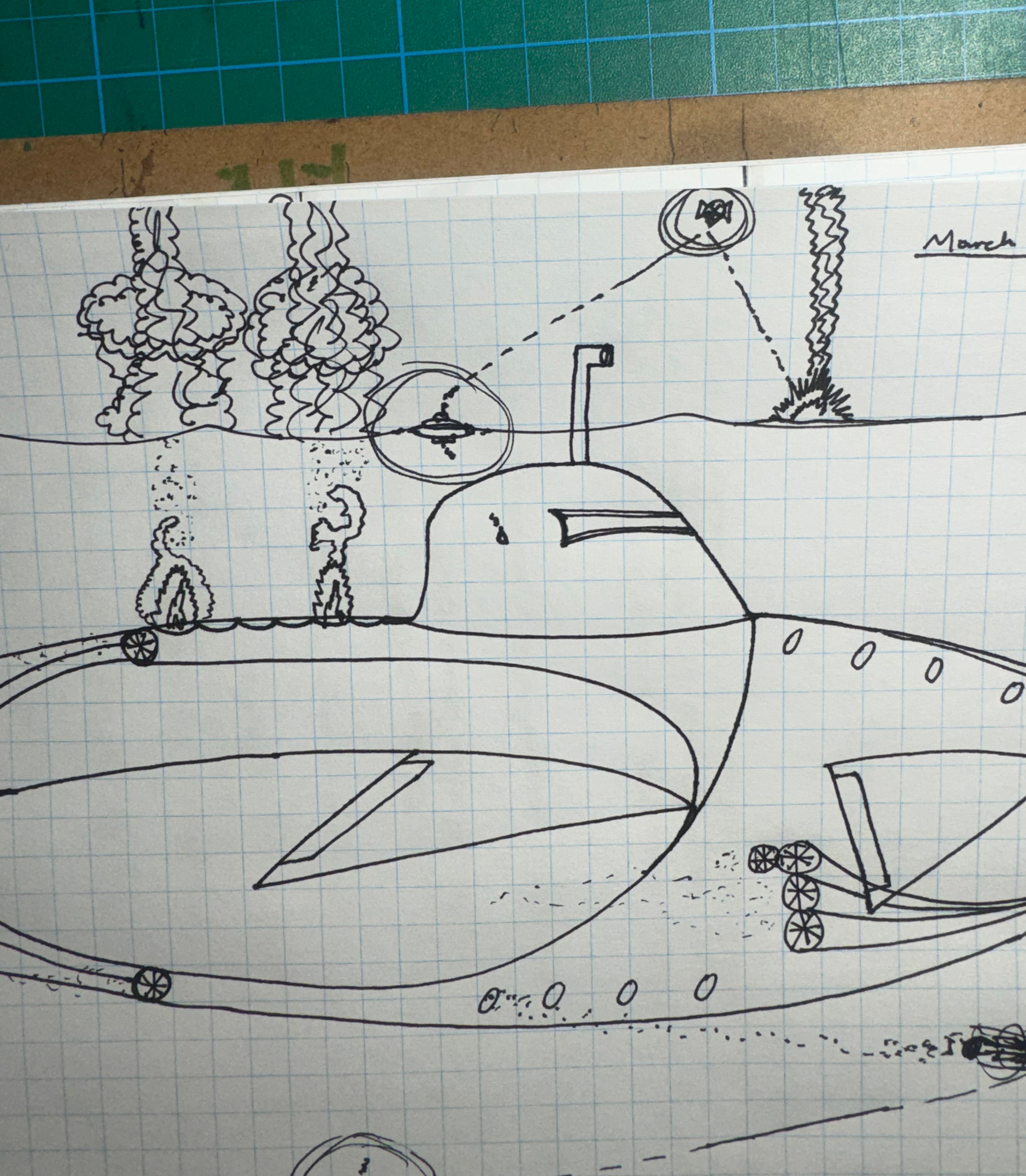
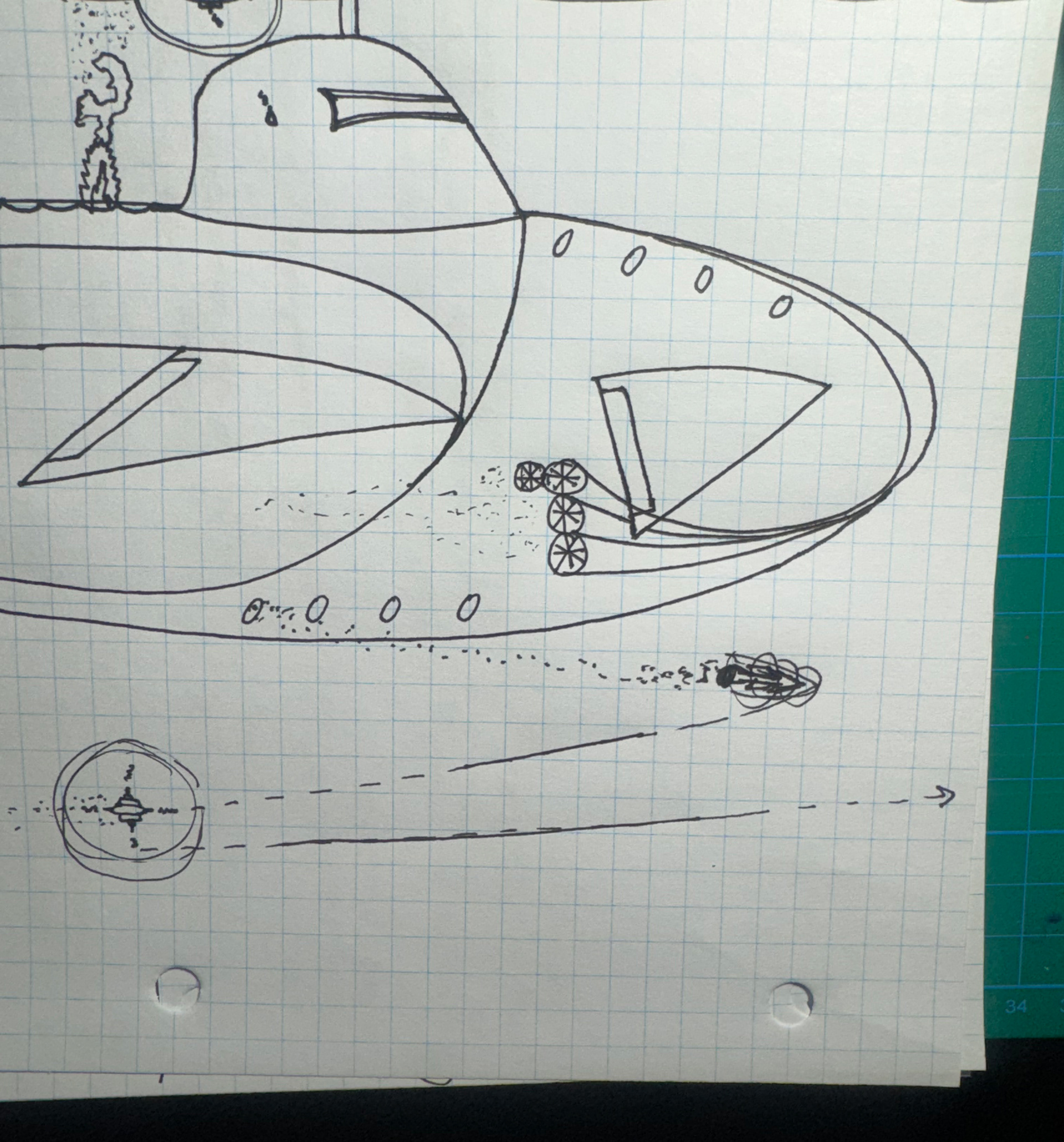
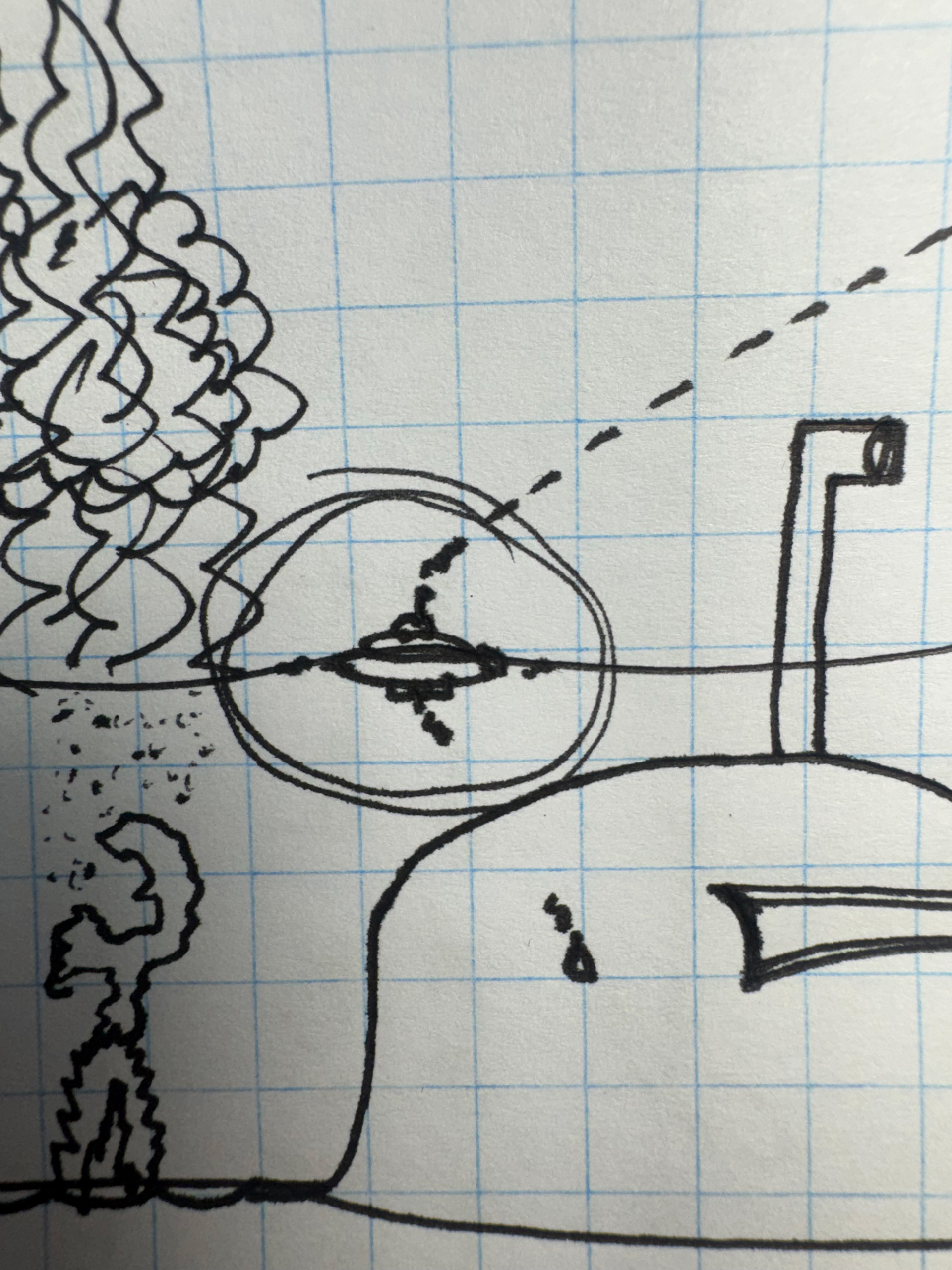
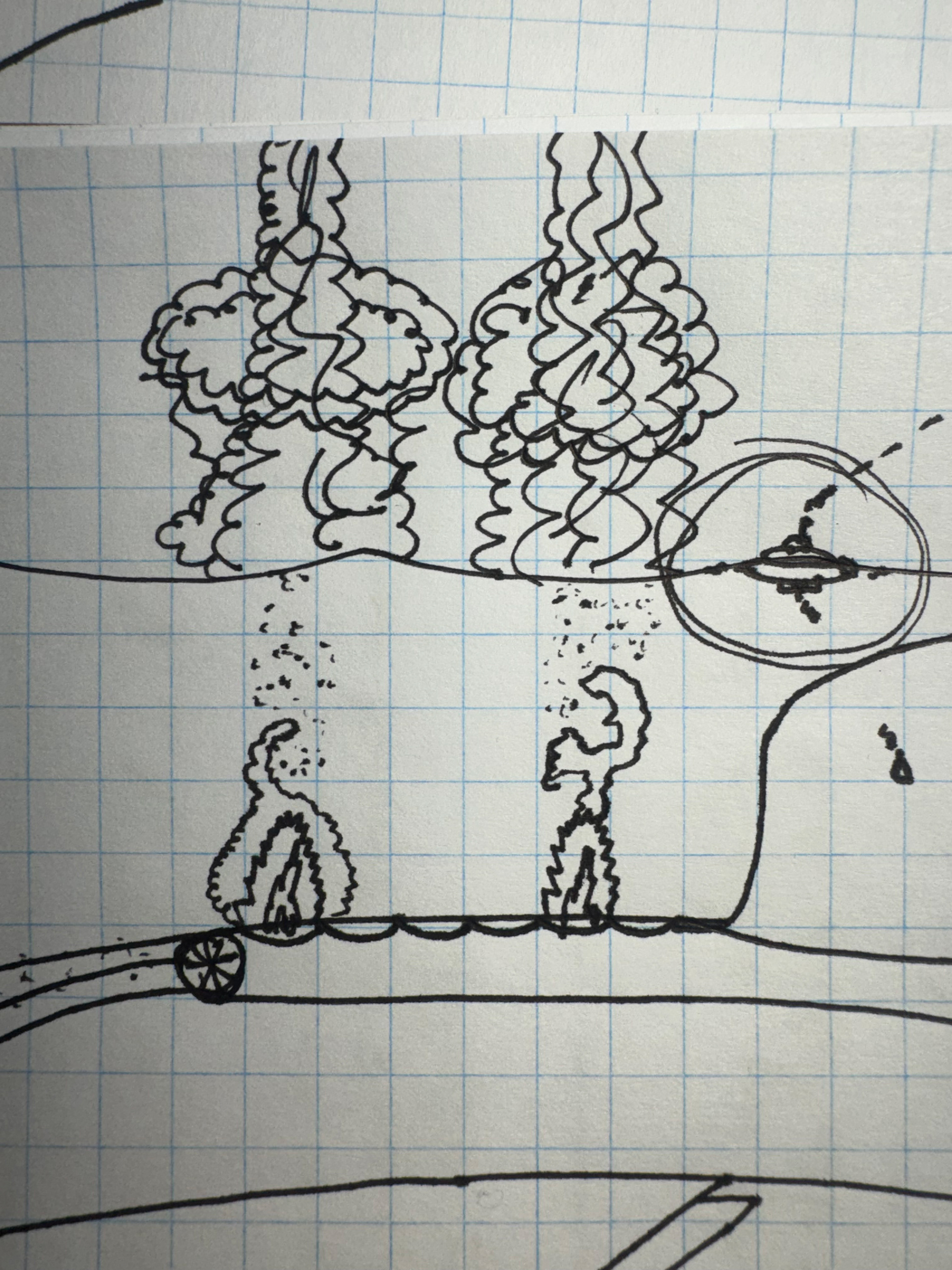

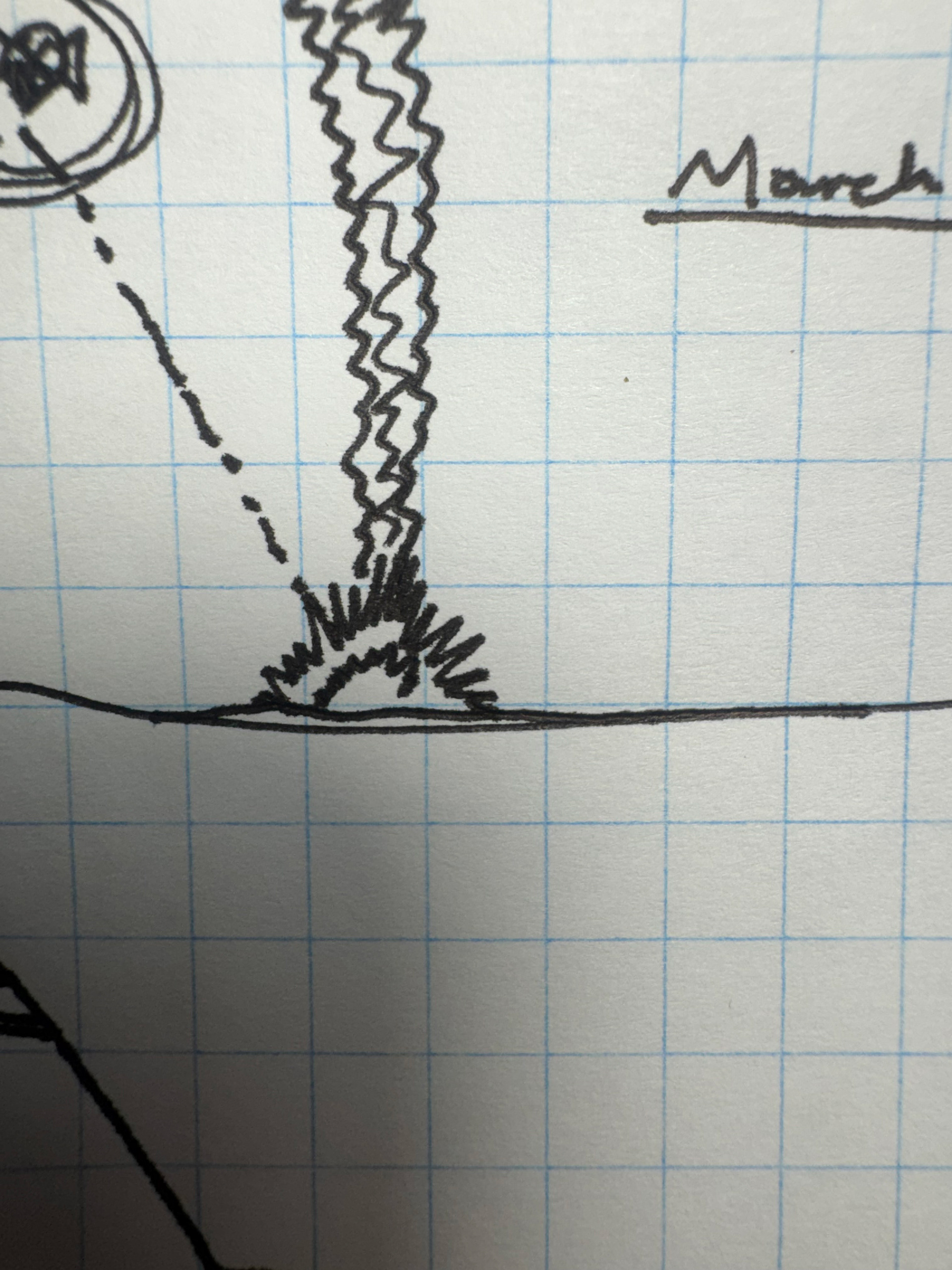
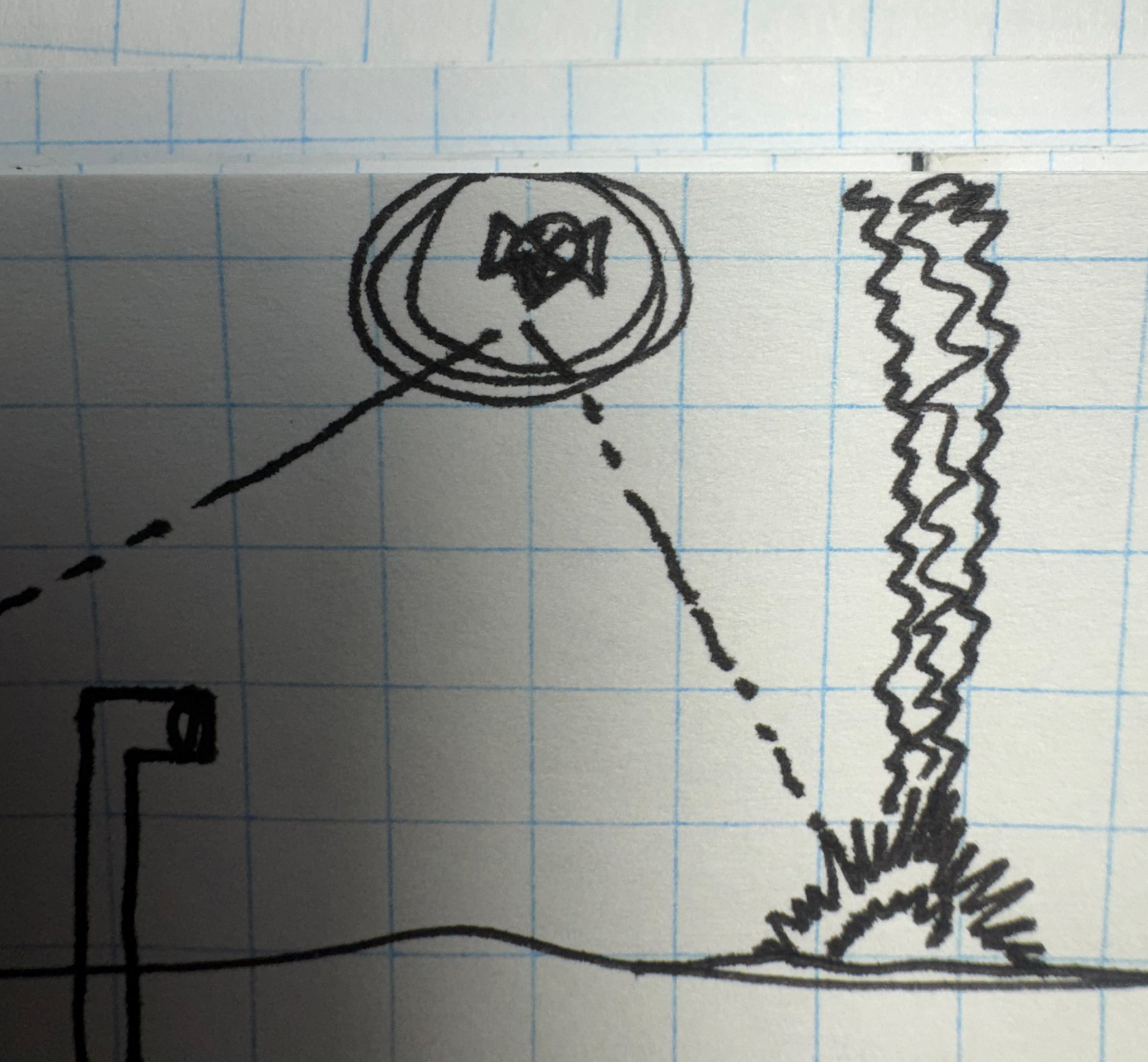
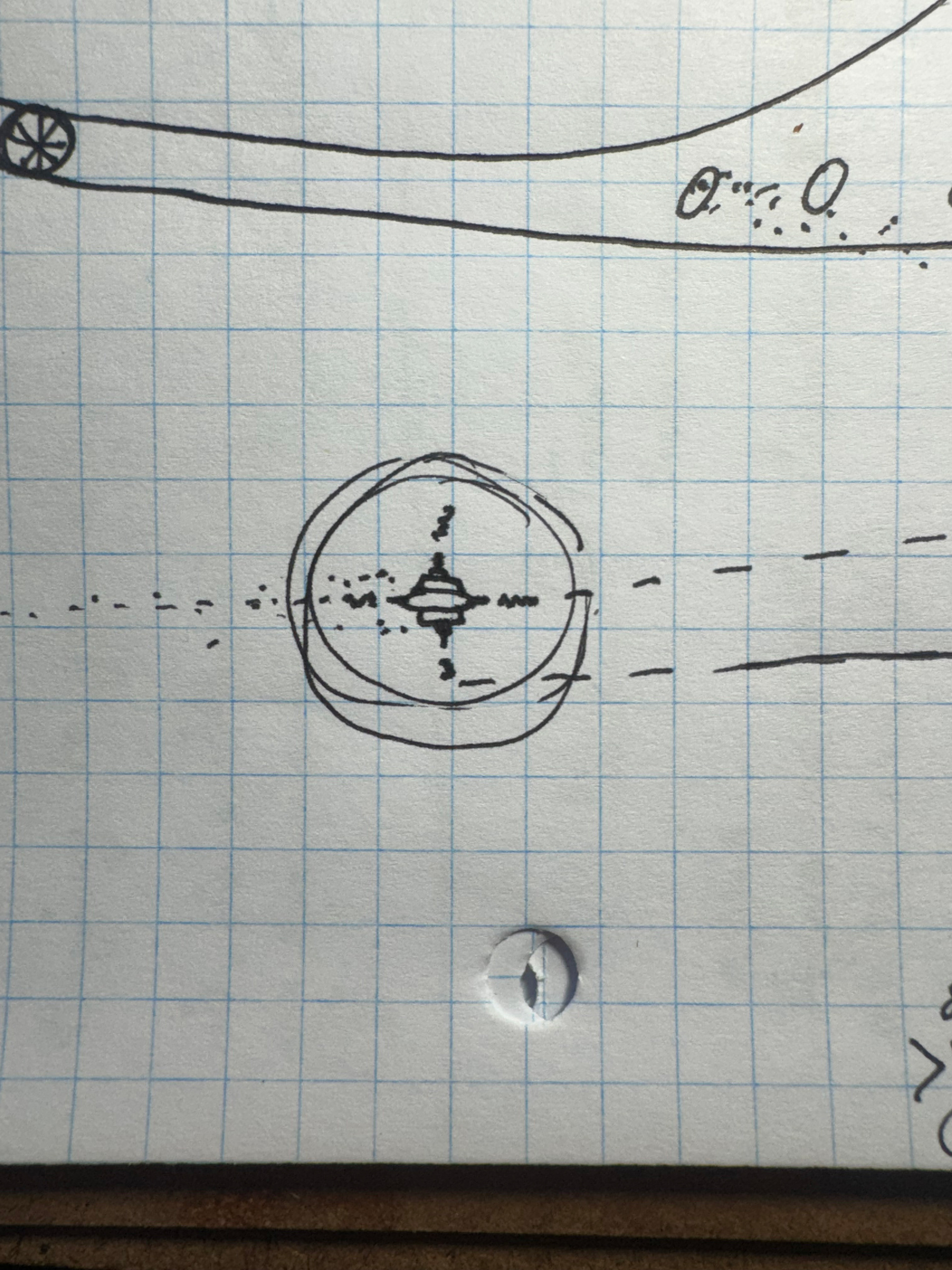
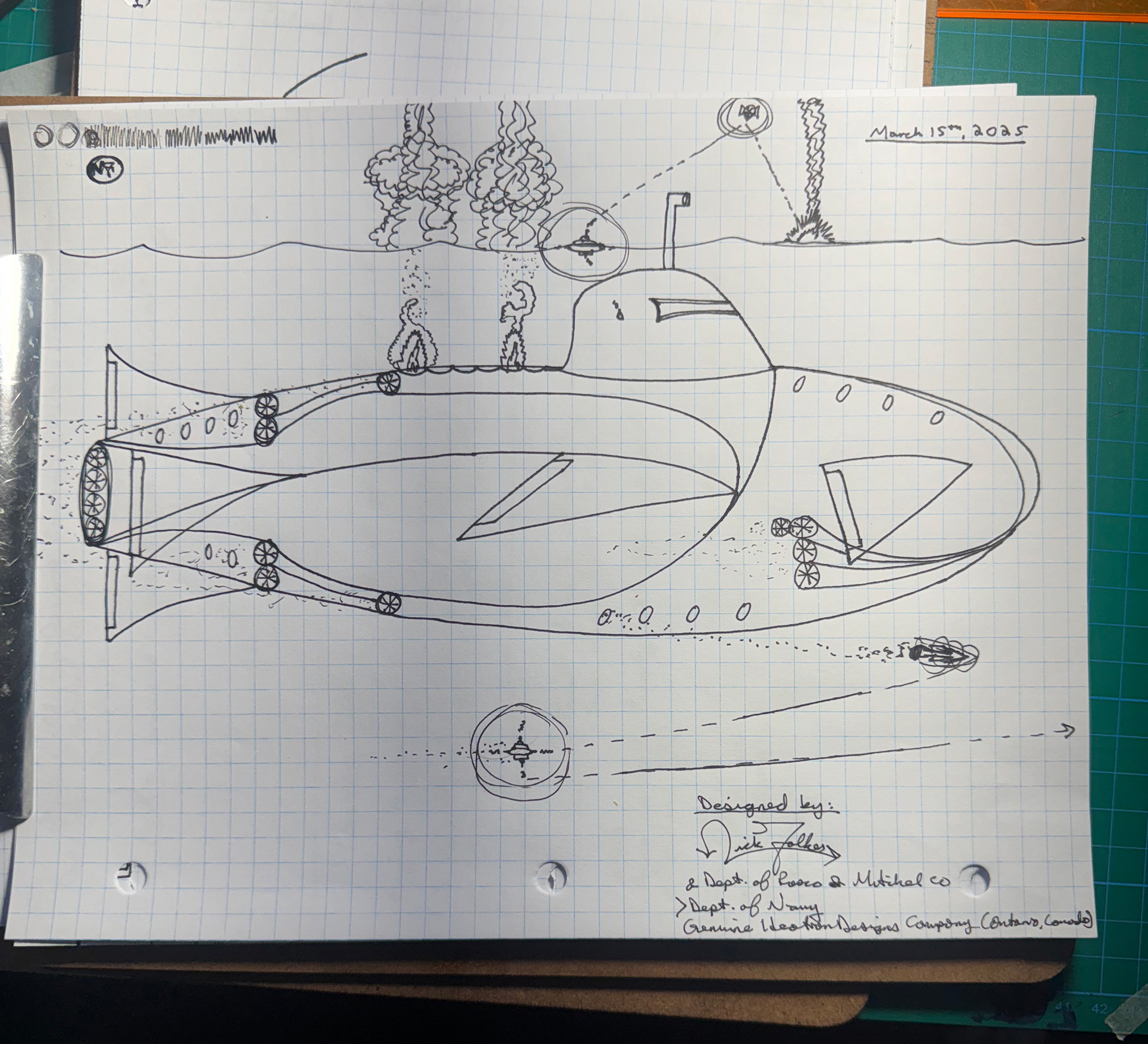
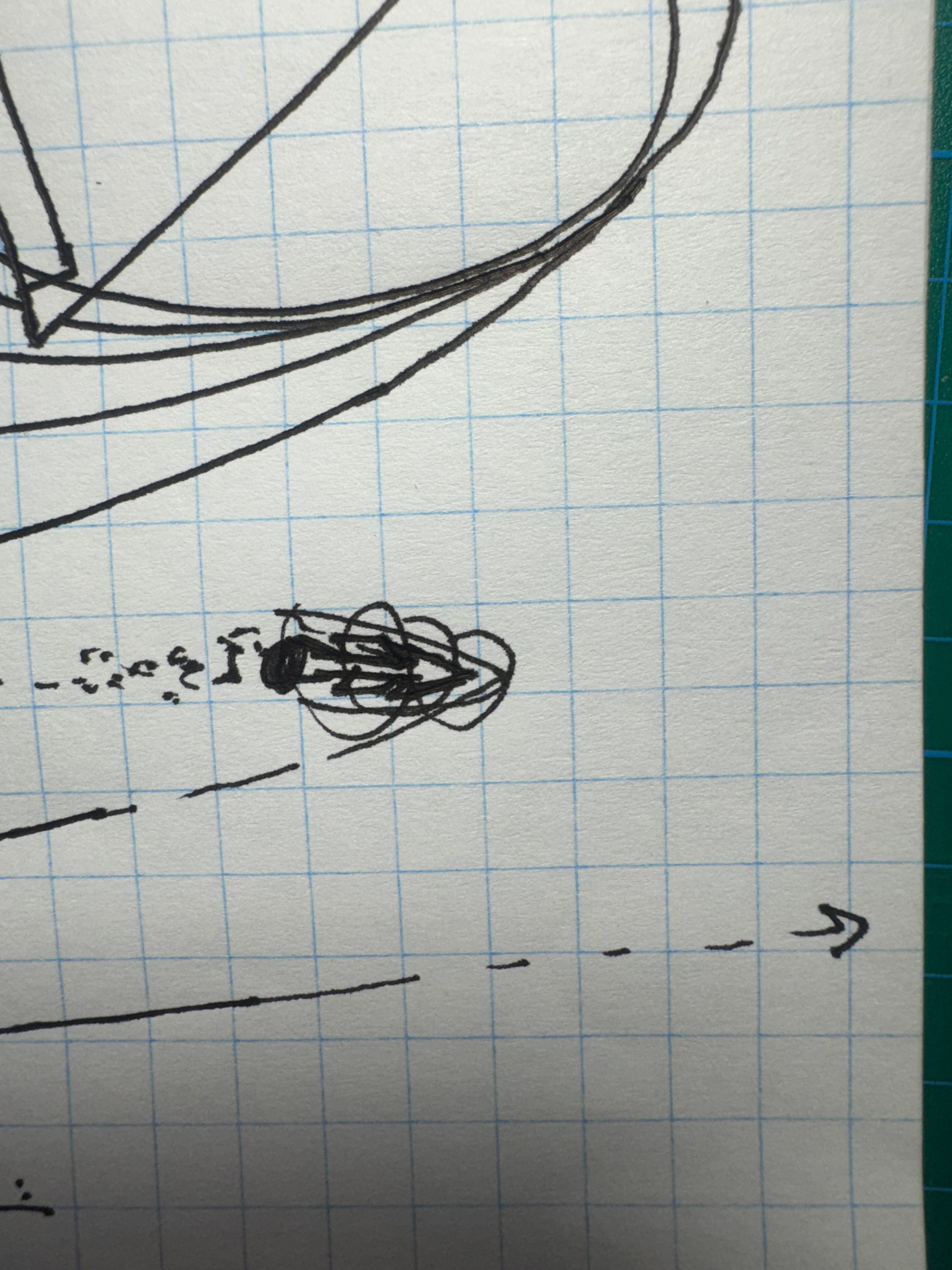
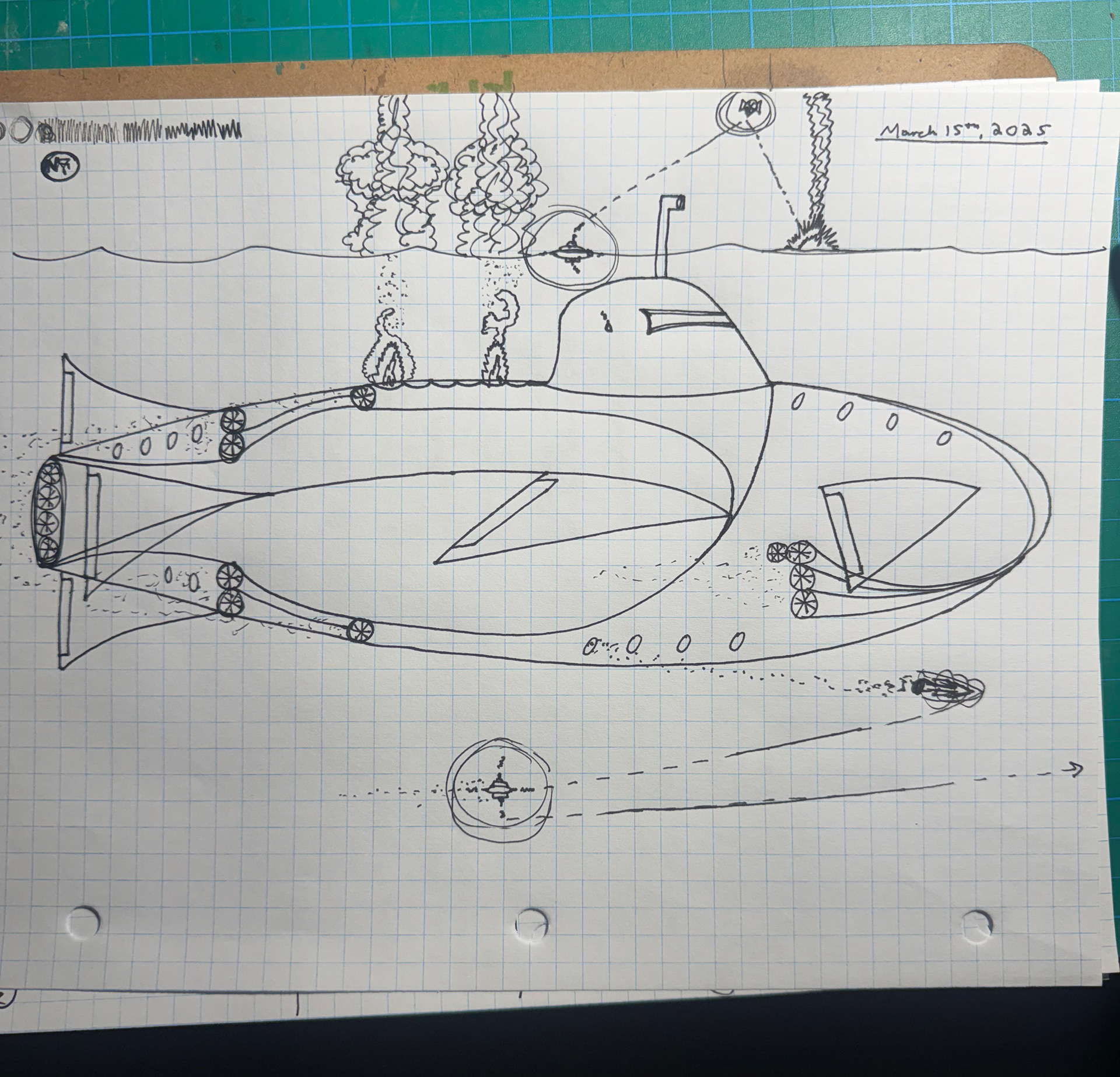
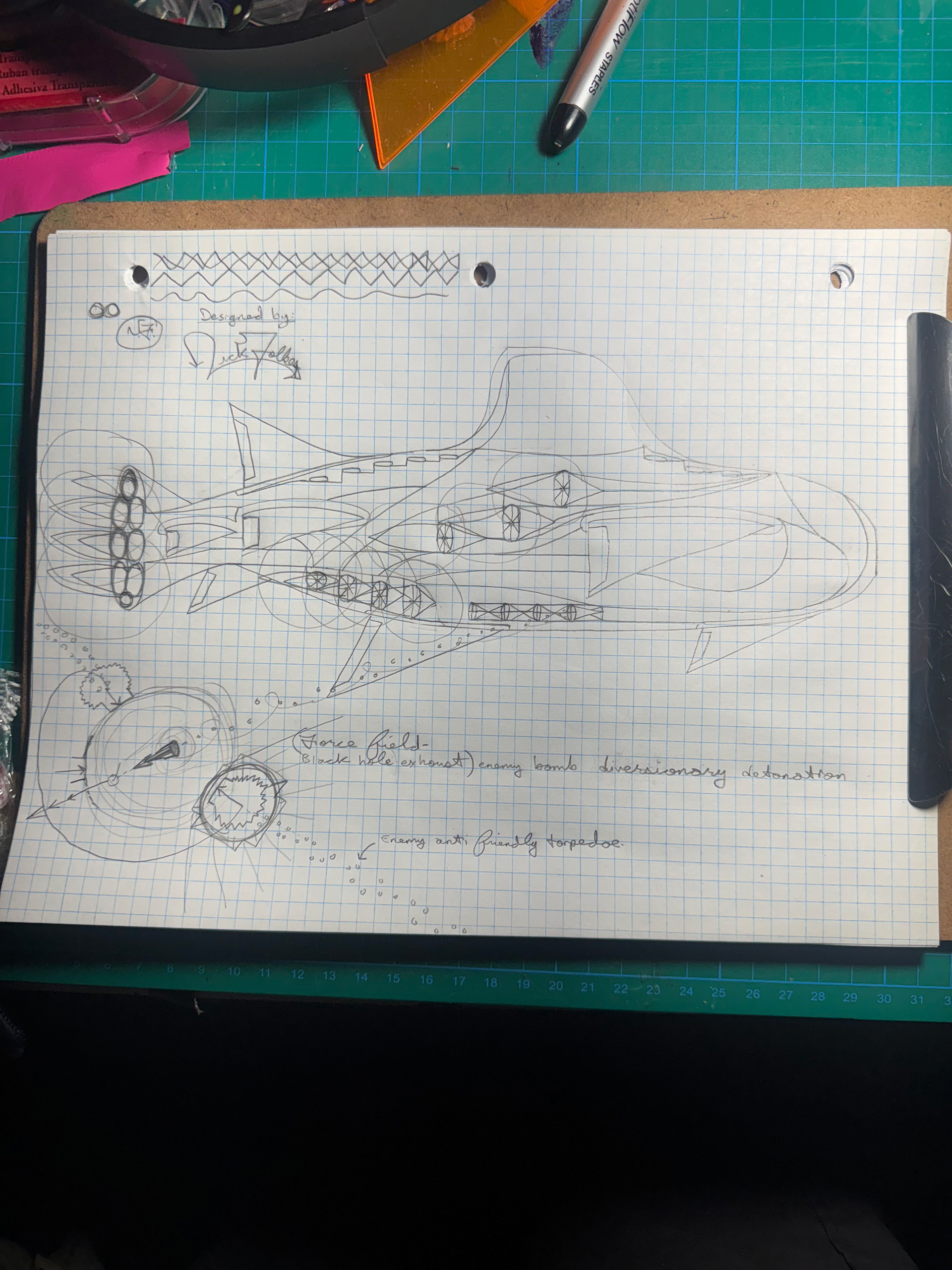
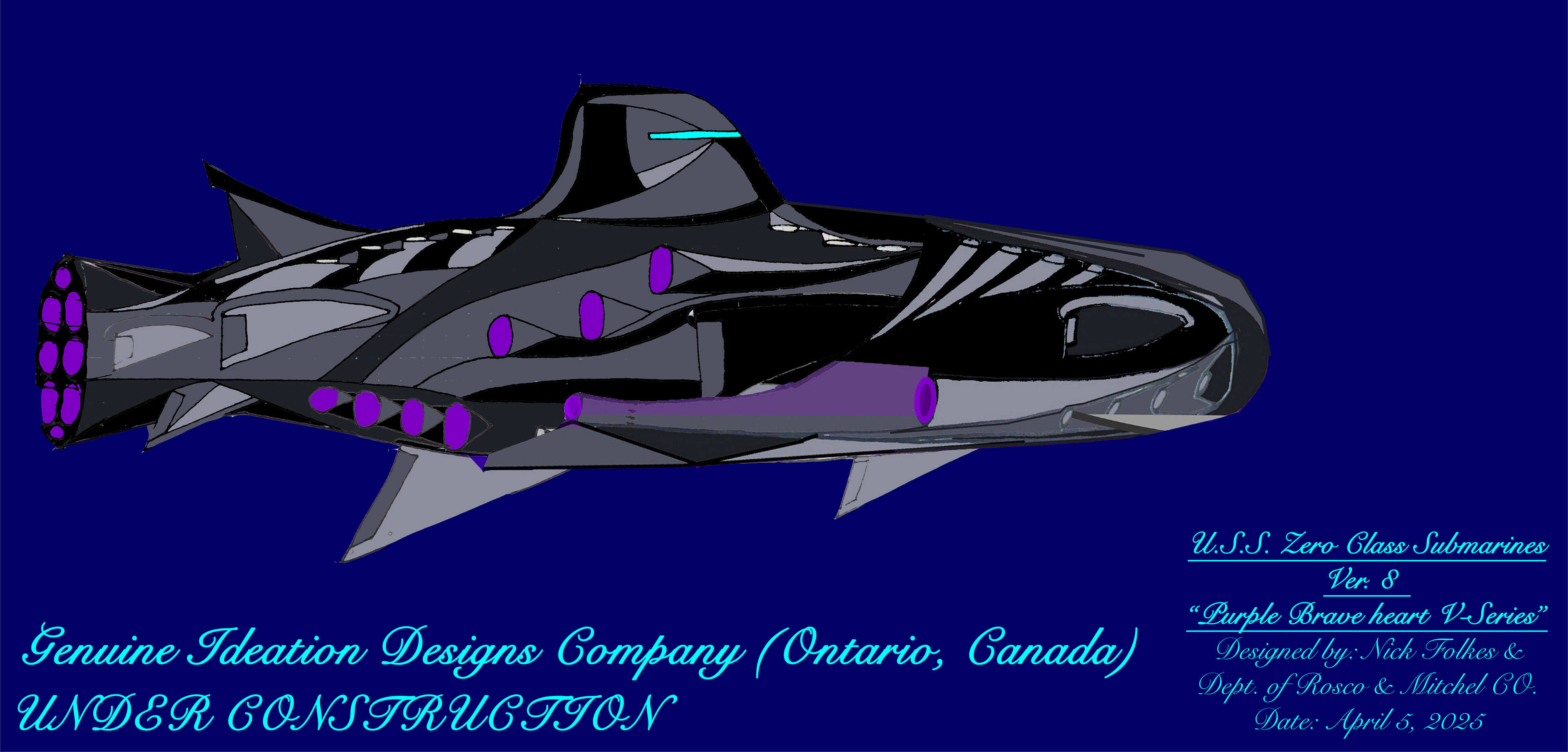
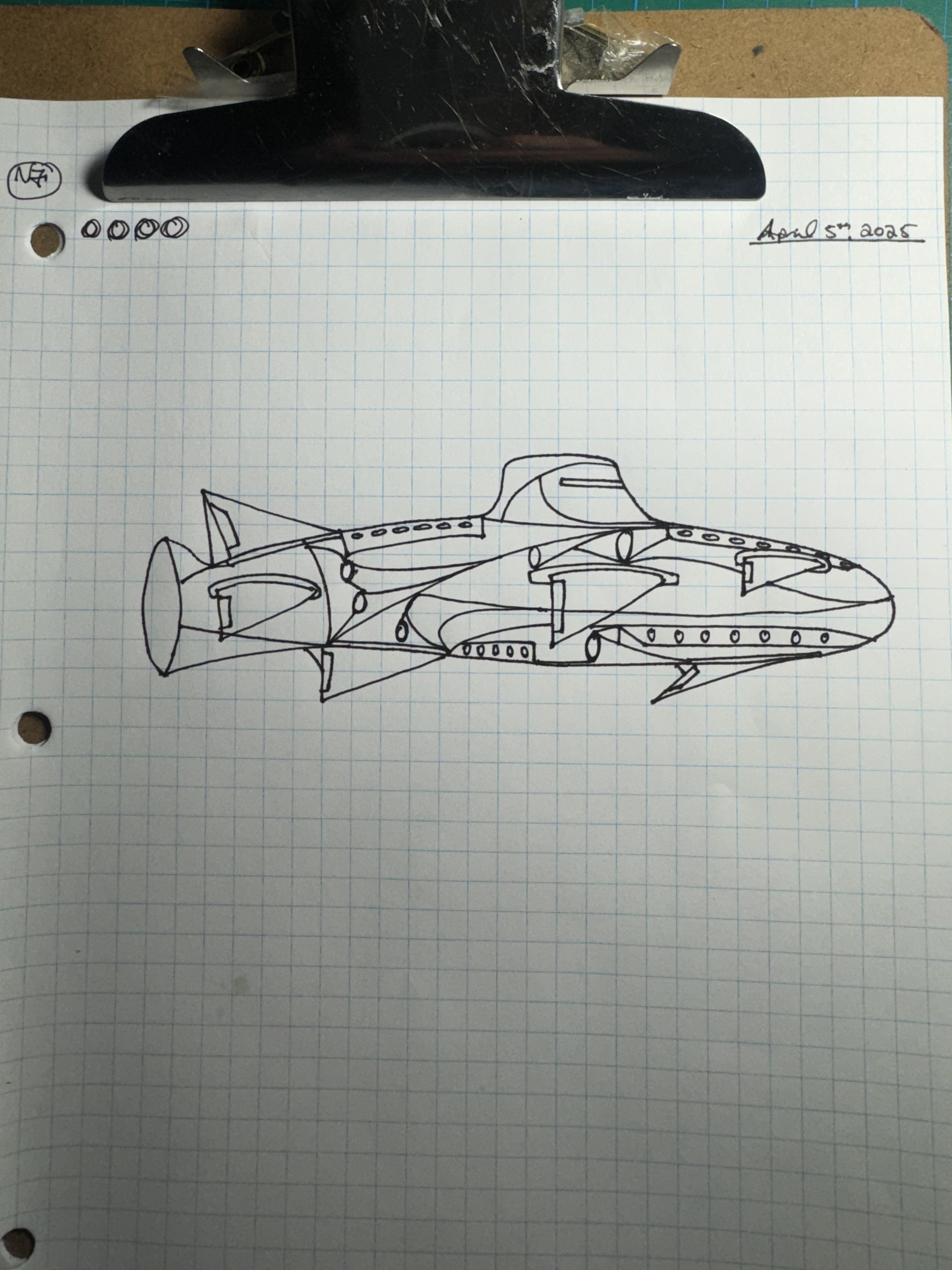
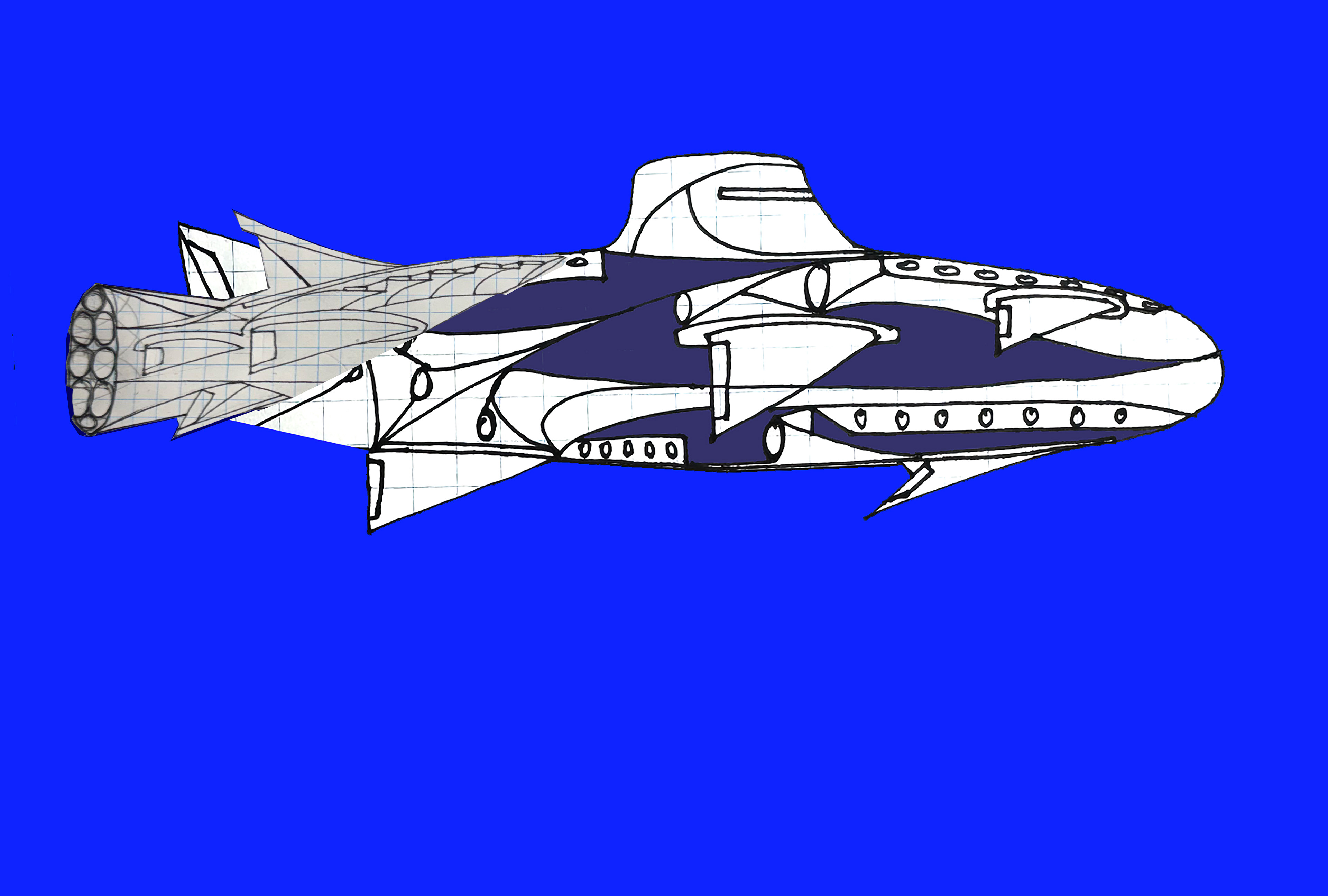
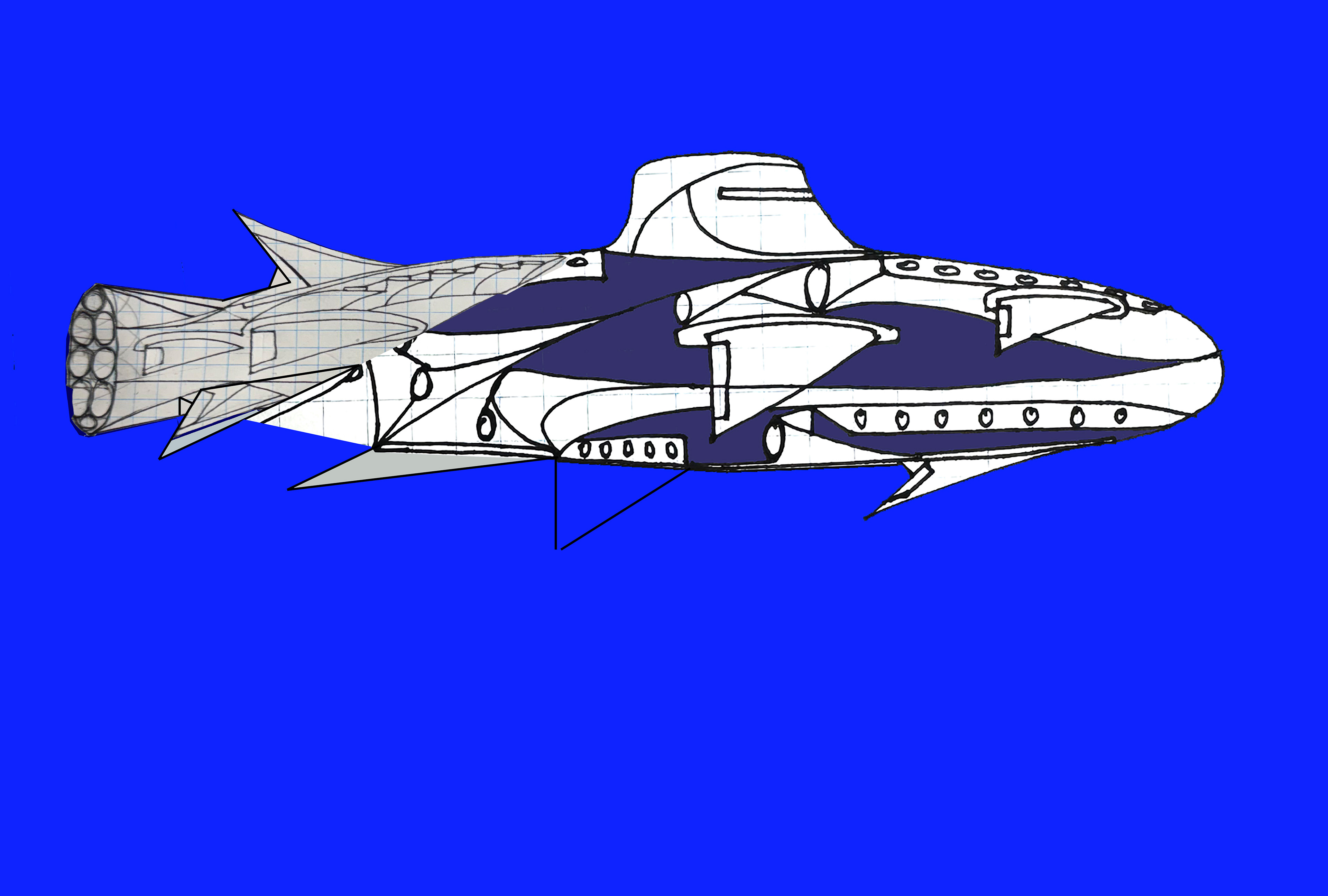
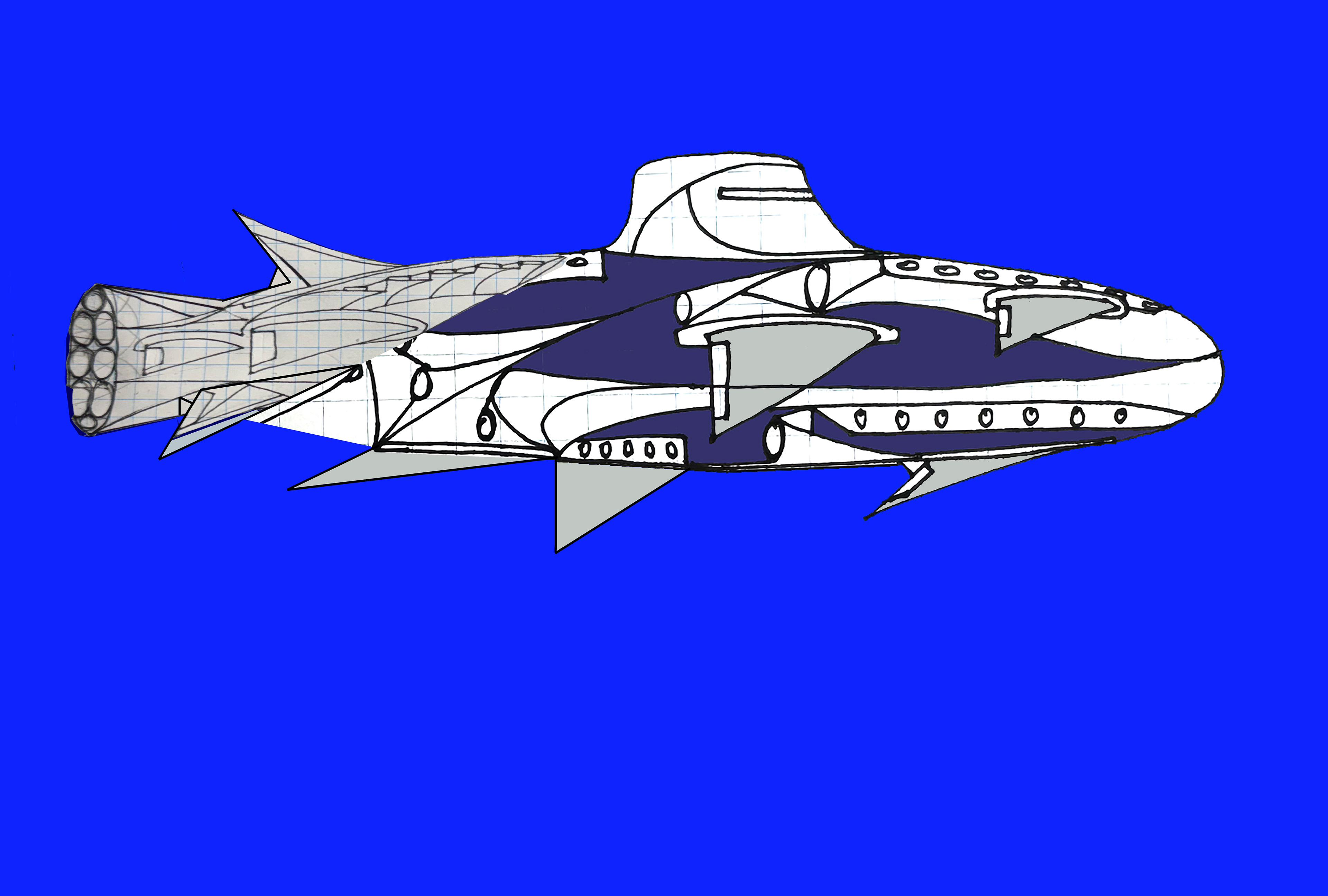
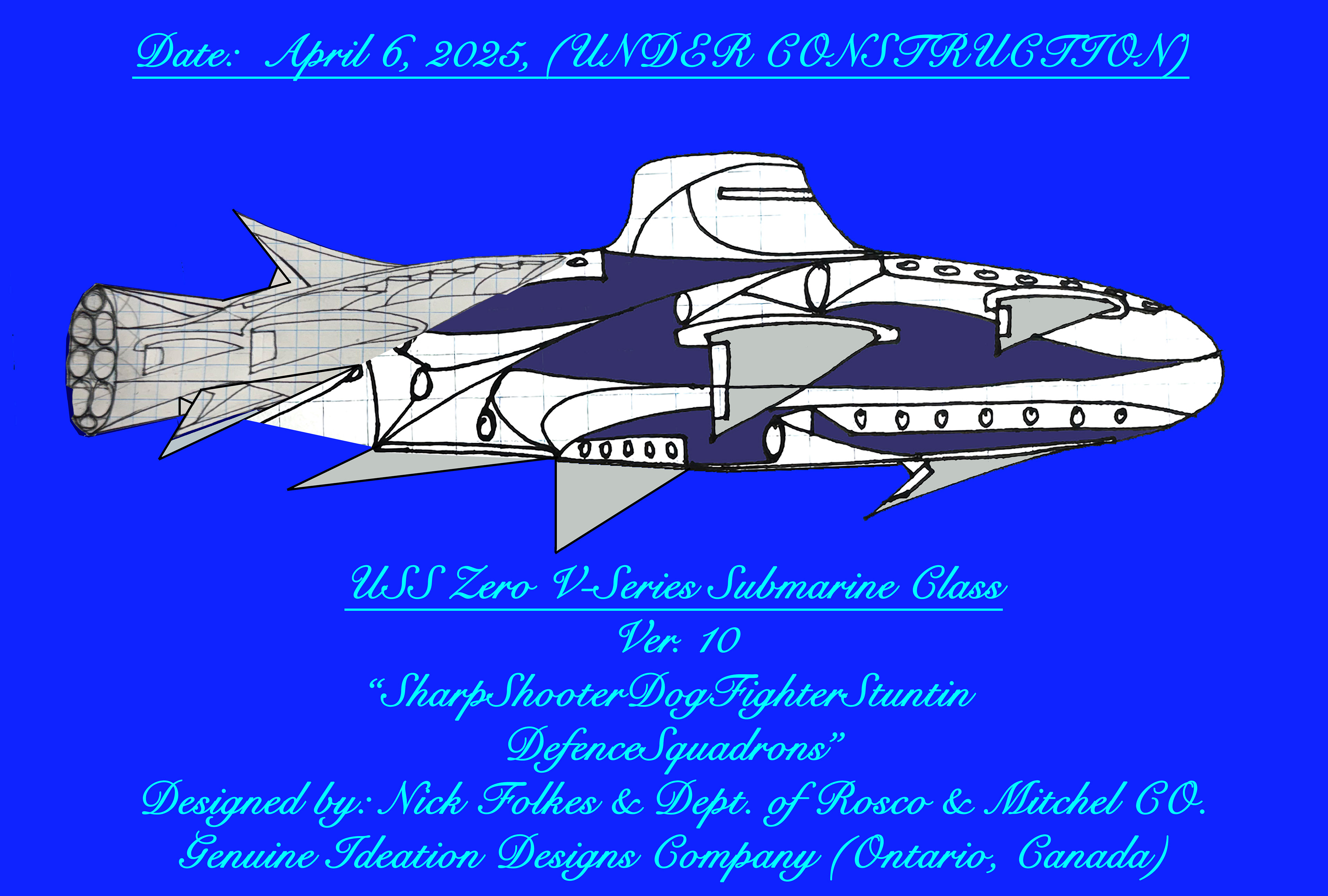
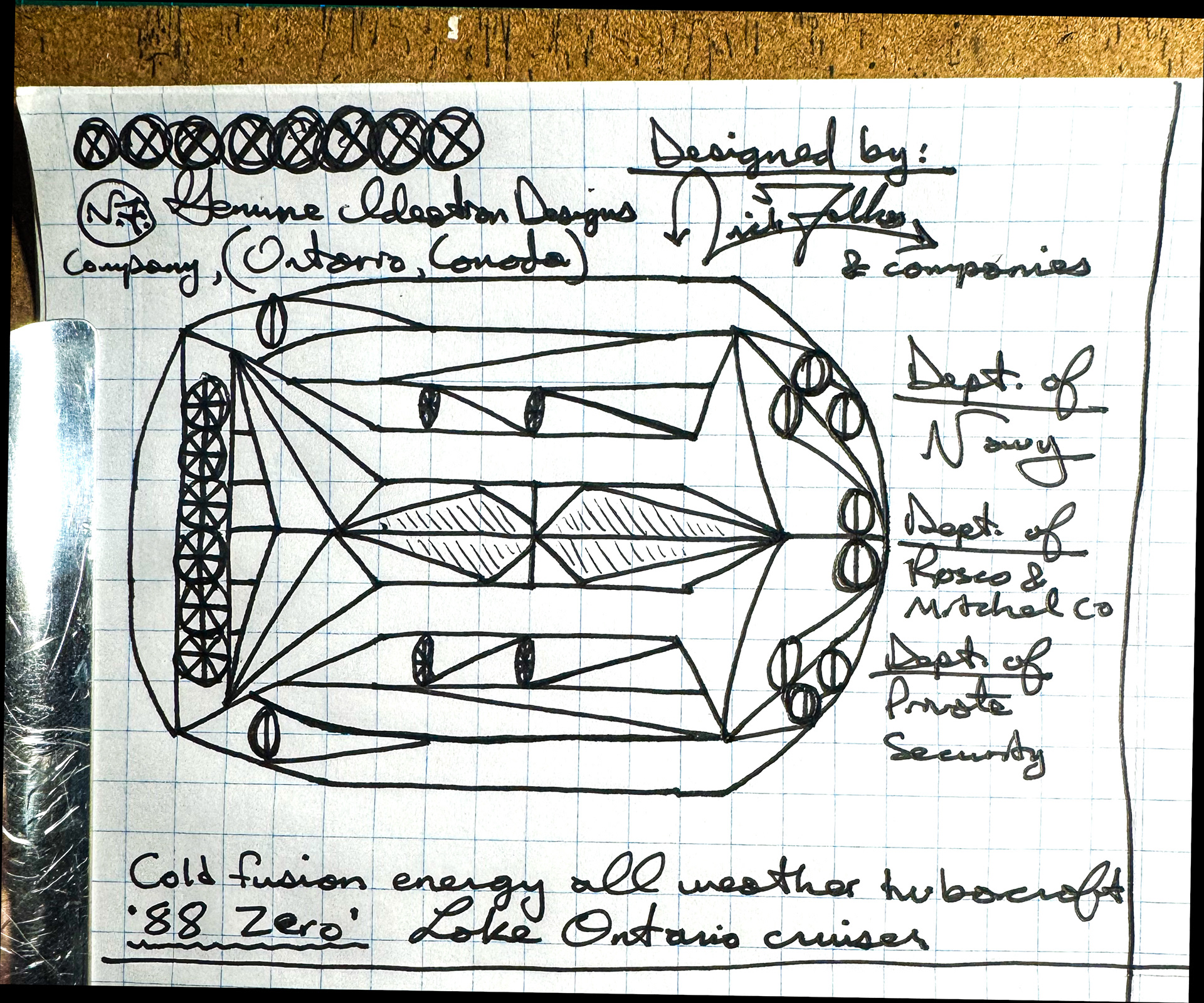
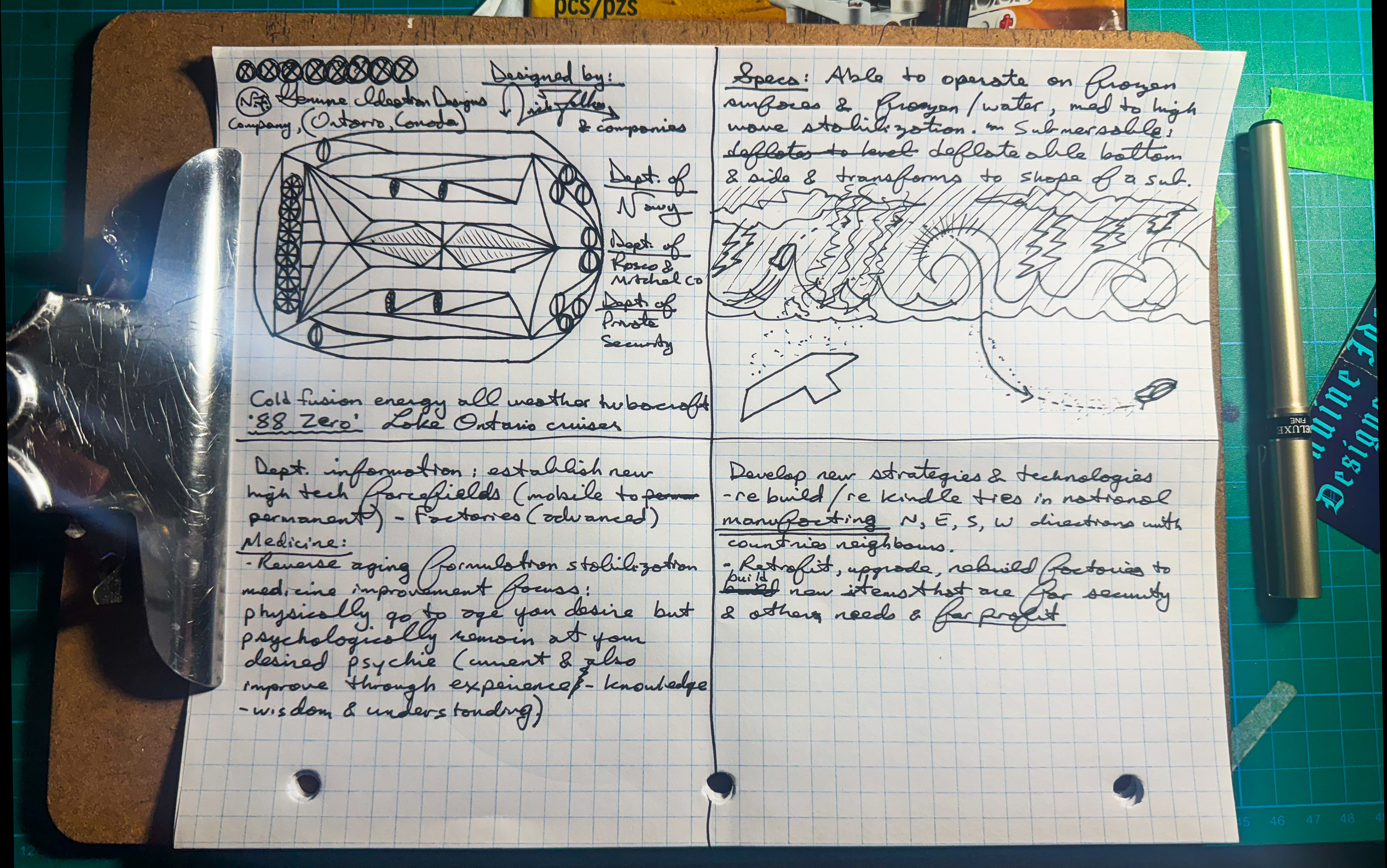
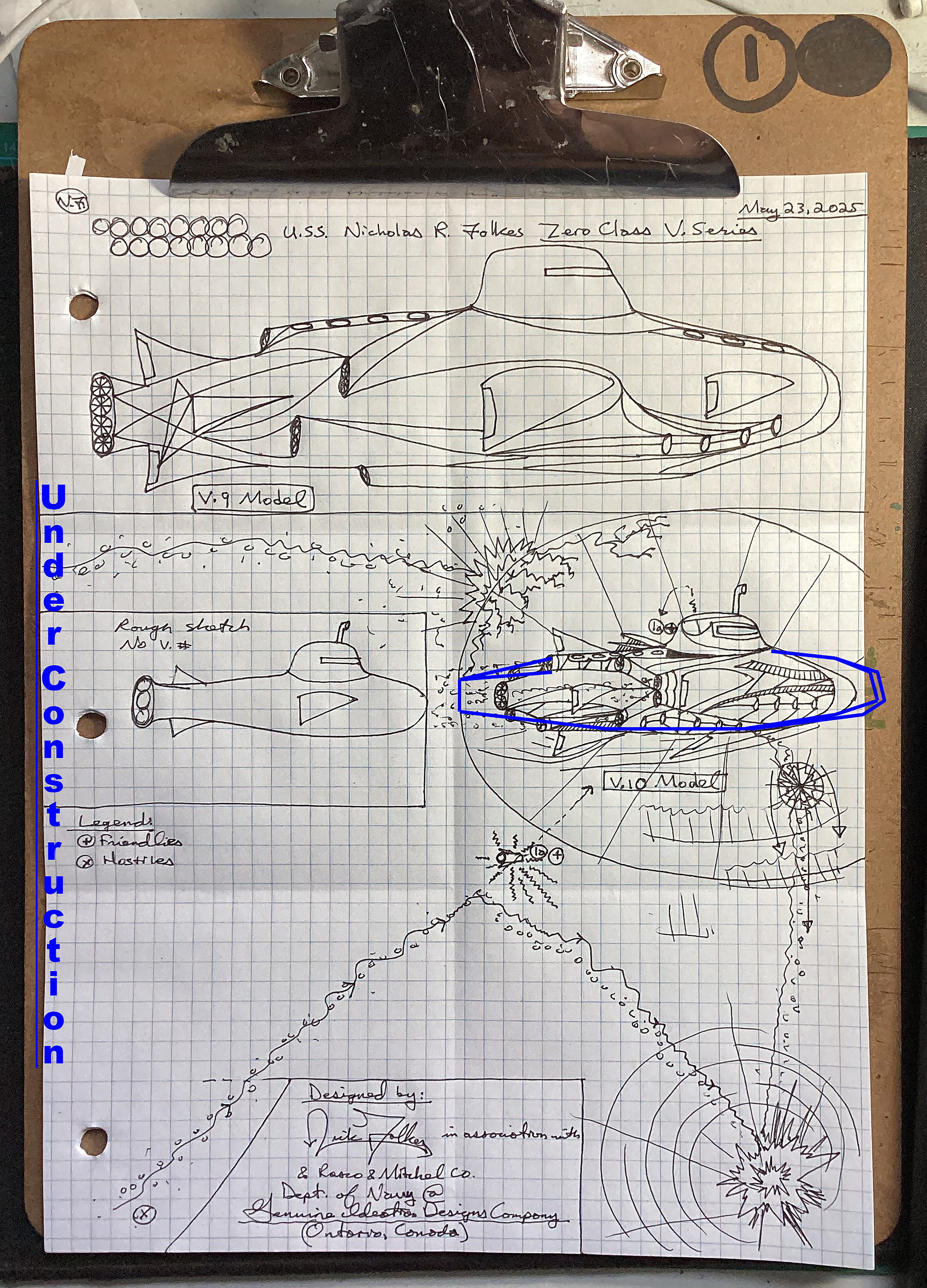
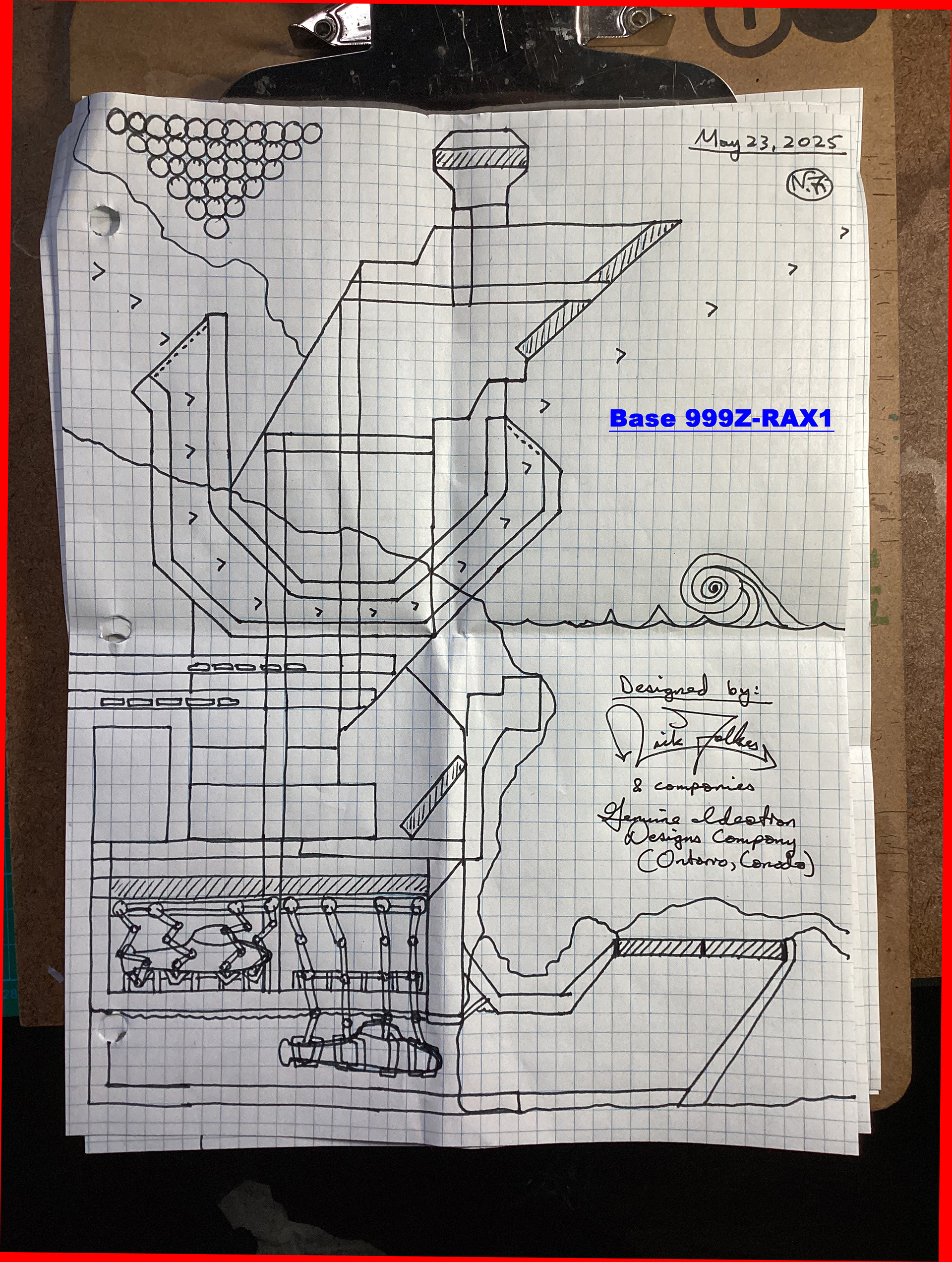
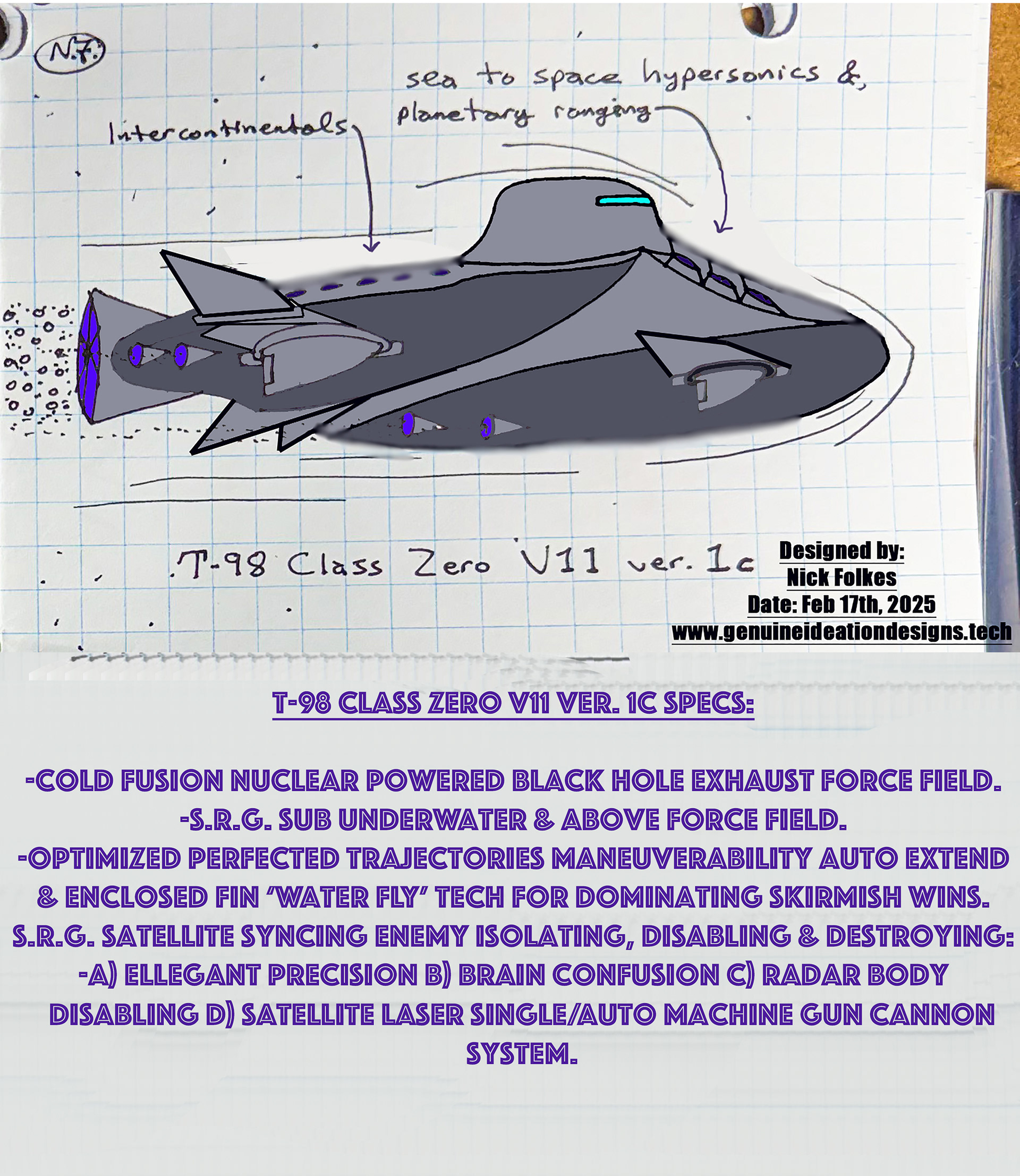
What is the most advanced futuristic enhanced high tech way to make this submarine design by Nick Folkes a reality? What are the scientific and mathematical methods and formulas required to make this happen?
What are the best strategies to utilize these submarine specs? What are modern very serious threats at sea and what are the best remedies to sort this into a winnable situation for this class of sub? What is the timeframe for all of these specs on this sub to take effect and become a full blown reality?
What is the best way to make multiple exact models of this 1 design? How can we best use adobe to 3dmax to AutoCAD engineers to have an exact precise blueprint to built this through? Are there any better methods to do this then that?
----------
To make Nick Folkes' T-98 Class Zero V11 sub design a reality, multiple scientific and technological disciplines must come together. Here are the key aspects and approaches that would need to be followed:
Scientific and Mathematical Methods
Cold Fusion Nuclear Power:
Cold fusion would require advanced breakthroughs in nuclear physics, specifically regarding controlled fusion reactions at room temperature. Methods like the Lattice-assisted nuclear reaction (LANR) have been proposed, though they remain highly controversial and unproven.
A combination of quantum mechanics and material science would be crucial here. Mathematically, quantum tunneling and fusion cross-sections would need to be modeled to simulate energy production.
Black Hole Exhaust Force Field:
This could theoretically involve manipulating gravitational fields or electromagnetic fields at the subatomic level, perhaps drawing from research on Hawking radiation or electrostatic repulsion in materials. Numerical modeling of general relativity would be needed to simulate such forces.
Hydrodynamics and Trajectory Optimization:
The design's underwater and above-water capabilities would require optimized hydrodynamic modeling, likely using Computational Fluid Dynamics (CFD). This would involve calculating drag, buoyancy, and stability factors, combined with optimal trajectory algorithms for speed and fuel efficiency. Equations like the Reynolds number and Navier-Stokes equations for fluid flow are key.
Water Fly Technology:
For this tech to exist, a deep understanding of fluid dynamics, jet propulsion, and the principles behind unconventional flight technologies would be needed. Engineering high-thrust actuators and dynamic stabilization systems for underwater and aerial flight (possibly a hybrid air/water system) would require innovative aerodynamic and hydrodynamic simulations.
For this tech to exist, a deep understanding of fluid dynamics, jet propulsion, and the principles behind unconventional flight technologies would be needed. Engineering high-thrust actuators and dynamic stabilization systems for underwater and aerial flight (possibly a hybrid air/water system) would require innovative aerodynamic and hydrodynamic simulations.
Brain Confusion and Electronic Warfare:
For this feature, a combination of neuro-engineering, electromagnetic radiation manipulation, and AI-based electronic warfare systems would be required. Techniques like signal jamming, hacking satellite communication systems, and possibly transcranial magnetic stimulation (TMS) could be involved in confusing enemy personnel. These systems would need to be backed by strong mathematical models to assess their range, power, and interference patterns.
Modern Sea Threats
Anti-Submarine Warfare (ASW):
Modern threats include submarine detection systems (active sonar, passive sonar, satellite detection), torpedoes, and anti-submarine drones.
Remedies could involve:
Using stealth technologies like active camouflage: Mirror formulate cloack-confuse water masking chameleonics (M.F.C.W.M.C.C.'s) I.e. (MCWIMICS) and silence systems to avoid sonar detection.
Advanced electromagnetic shielding or decoys to confuse enemy sonar.
Deployment of countermeasure drones for defense against torpedoes and drones.
Nuclear and Electromagnetic Pulse (EMP) Weapons:
These could disrupt the submarine's electronics.
These could disrupt the submarine's electronics.
Remedies:
Hardening electronics with EMP-resistant materials.
Creating redundant systems with electromagnetic isolation.
Cybersecurity Threats:
The sub's advanced systems would be vulnerable to hacking.
Remedies:
Implementing quantum encryption and AI-driven anomaly detection to prevent hacking attempts.
Timeframe to Reality
Achieving this level of technology would likely take several decades. Key milestones:
Cold Fusion: This could take 20-50 years to become viable if breakthroughs occur.
Black Hole Exhaust and Force Field Technology: Likely many decades to potentially centuries, depending on scientific breakthroughs.
Advanced Underwater-Aerial Propulsion: This could take 10-20 years, as research into amphibious or dual-environment craft is ongoing.
Electronic Warfare Capabilities: Could be implemented in a decade or so, depending on advances in AI and neuromodulation.
Creating Multiple Models of the Design
To create multiple exact models:
3D Scanning: Use 3D scanners to digitize the initial prototype model.
Rapid Prototyping: Utilize 3D printing (preferably metal 3D printing) for the rapid creation of physical models.
Precision Engineering: To ensure exact replicas, use CNC milling for parts that require high precision.
Best Software and Workflow for Engineering
AutoCAD for detailed 2D blueprints and 3D modeling of complex systems.
SolidWorks for mechanical design and simulation.
Blender or Maya for highly detailed visual rendering and animation.
Adobe for project management, presentation, and design conceptualization.
ANSYS or COMSOL for fluid dynamics simulations, structural integrity, and other scientific modeling.
Best Approach for Precision
While AutoCAD and 3D Max are standard tools, consider integrating parametric design tools (e.g., Rhinoceros 3Dwith Grasshopper) for creating adaptable, mathematically derived designs. Collaborative platforms like Fusion 360and CATIA also integrate with engineering, prototyping, and simulation tools, making them ideal for team-based work.
------
Other imperatives for construction of this design;
Creating Multiple Exact Models of the T-98 Class Zero V11 Submarine
To mass-produce exact replicas of this advanced submarine, a multi-step approach integrating 3D scanning, rapid prototyping, precision engineering, and automated manufacturing is required. Below is a breakdown of the best methodologies.
1. 3D Scanning for Digital Model Creation
Before manufacturing, a high-precision 3D scan of the design is necessary to ensure every curve, surface, and functional element is digitally preserved.
Best Technologies for 3D Scanning:
Structured Light Scanners: Best for high-detail scanning of small-to-medium components.
LiDAR Scanners: Excellent for scanning large-scale objects like a submarine hull.
Photogrammetry: Captures ultra-detailed geometry using high-resolution cameras and AI to stitch together a precise 3D model.
Contact CMM (Coordinate Measuring Machine): Provides ultra-precise measurements of individual mechanical parts.
Best 3D Scanning Software:
Geomagic Design X – Converts scan data into parametric CAD models.
PolyWorks – Ideal for inspection and reverse engineering.
Autodesk ReCap – Converts LiDAR scans into detailed 3D models.
2. Rapid Prototyping for Physical Model Validation
Once the 3D model is generated, rapid prototyping allows for the creation of scaled or full-size models to test aerodynamics, hydrodynamics, and material integrity.
Best Technologies for Rapid Prototyping:
Metal 3D Printing (DMLS or SLM)
Direct Metal Laser Sintering (DMLS) and Selective Laser Melting (SLM) can produce full-scale metal prototypes.
Best for complex internal geometries, lightweight structures, and functional testing.
Polymer 3D Printing for Concept Models
Stereolithography (SLA) & Fused Deposition Modeling (FDM) for non-metal parts.
Used for small-scale aerodynamic and hydrodynamic testing.
Carbon Fiber Printing (Markforged X7)
Can create lightweight, strong parts for high-performance aerospace applications.
Best Rapid Prototyping Software:
Fusion 360 – Integrates CAD, CAM, and simulation for prototype testing.
Materialise Magics – Prepares 3D prints with error correction.
ANSYS Additive – Simulates stress analysis for 3D printed metal parts.
3. Precision Engineering for Exact Replication
After validating the prototype, precision engineering ensures exact duplication of each submarine part.
Best Manufacturing Methods:
CNC Milling for High-Precision Parts
5-axis CNC machining ensures sub-micron accuracy.
Titanium, carbon fiber, and advanced alloys are milled for structural integrity.
Injection Molding for Non-Metal Components
Used for producing thousands of identical polymer-based parts.
Best for internal casings, soft-touch surfaces, and polymer composites.
Waterjet & Laser Cutting
Used for shaping thick steel or titanium plates.
Can create intricate heat-resistant panels for high-speed operation.
Automated Welding & Robotic Assembly
Advanced robotic welding ensures structural durability.
Autonomous assembly lines can produce multiple identical units efficiently.
Best Precision Engineering Software:
Siemens NX – Used by military contractors for high-precision parts.
CATIA – Aerospace-level precision for submarine interiors and systems.
Autodesk Powermill – Best for CNC machining and toolpath optimization.
4. Mass Production Strategies for Multiple Models
Once the engineering process is finalized, high-tech automation will be the key to efficiently producing multiple units.
Best Mass Production Methods:
Digital Twin Technology
A real-time digital replica of the submarine can be used for:
Predictive maintenance
Performance optimization
Automated adjustments during production
Best software: Siemens Digital Twin, Ansys Twin Builder.
Smart Factories with AI Automation
AI-driven robotic assembly optimizes manufacturing speed and cost reduction.
IoT (Internet of Things) integration allows for remote diagnostics of production errors.
Modular Assembly for Fast Replication
Submarines are built in pre-fabricated sections (hull, propulsion, command systems).
This reduces build time from years to months.
Additive Manufacturing Supply Chains
Instead of relying on traditional supply chains, 3D printing replacement parts directly in combat zones or onboard shipyards ensures continuous fleet sustainability.
5. 3D Modeling Workflow: From Adobe to 3ds Max to AutoCAD
To create an exact, precise blueprint, the following workflow can be followed:
Adobe Photoshop/Illustrator – Used for initial concept sketches and presentation designs.
Autodesk 3ds Max or Blender – Used for detailed 3D visualization and rendering.
AutoCAD or SolidWorks – Converts concept models into engineering blueprints.
Fusion 360 – Used for mechanical assembly and motion simulations.
ANSYS & CFD Software – Final hydrodynamic and aerodynamic testing.
Alternative & More Advanced Methods:
Generative AI Design
AI-driven design software (like Autodesk Dreamcatcher) can optimize structural geometryautomatically.
Quantum Computing for Simulations
Quantum simulation (using IBM Q or Google Sycamore) could analyze hydrodynamics at an atomic level.
Final Thoughts & Timeframe for Mass Production
Short-Term (1-5 Years):
Develop scaled prototypes with 3D printing.
Conduct hydrodynamic simulations and small-scale water flight tests.
Medium-Term (5-15 Years):
Cold fusion research may progress.
AI-controlled production lines for limited production models.
Long-Term (20+ Years):
Full-scale mass production with AI-driven automation.
Cold fusion power system integrated.
Satellite-controlled swarm systems operational.
Conclusion
By combining 3D scanning, metal 3D printing, CNC milling, and automated AI-based assembly lines, exact multiple models of the T-98 Class Zero submarine can be replicated at scale. Digital Twin Technology, AI-driven manufacturing, and smart modular production will make mass production fast and precise.
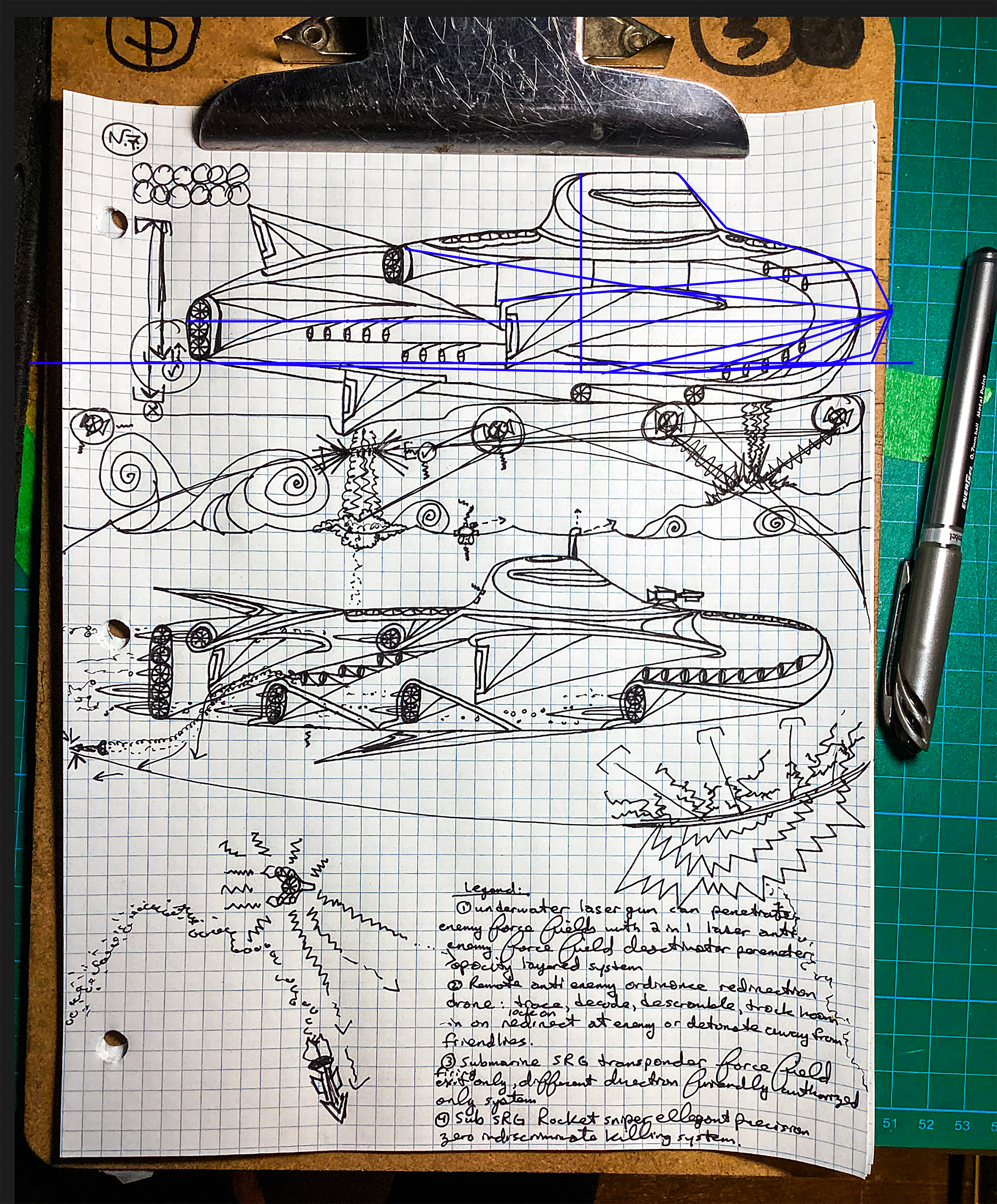
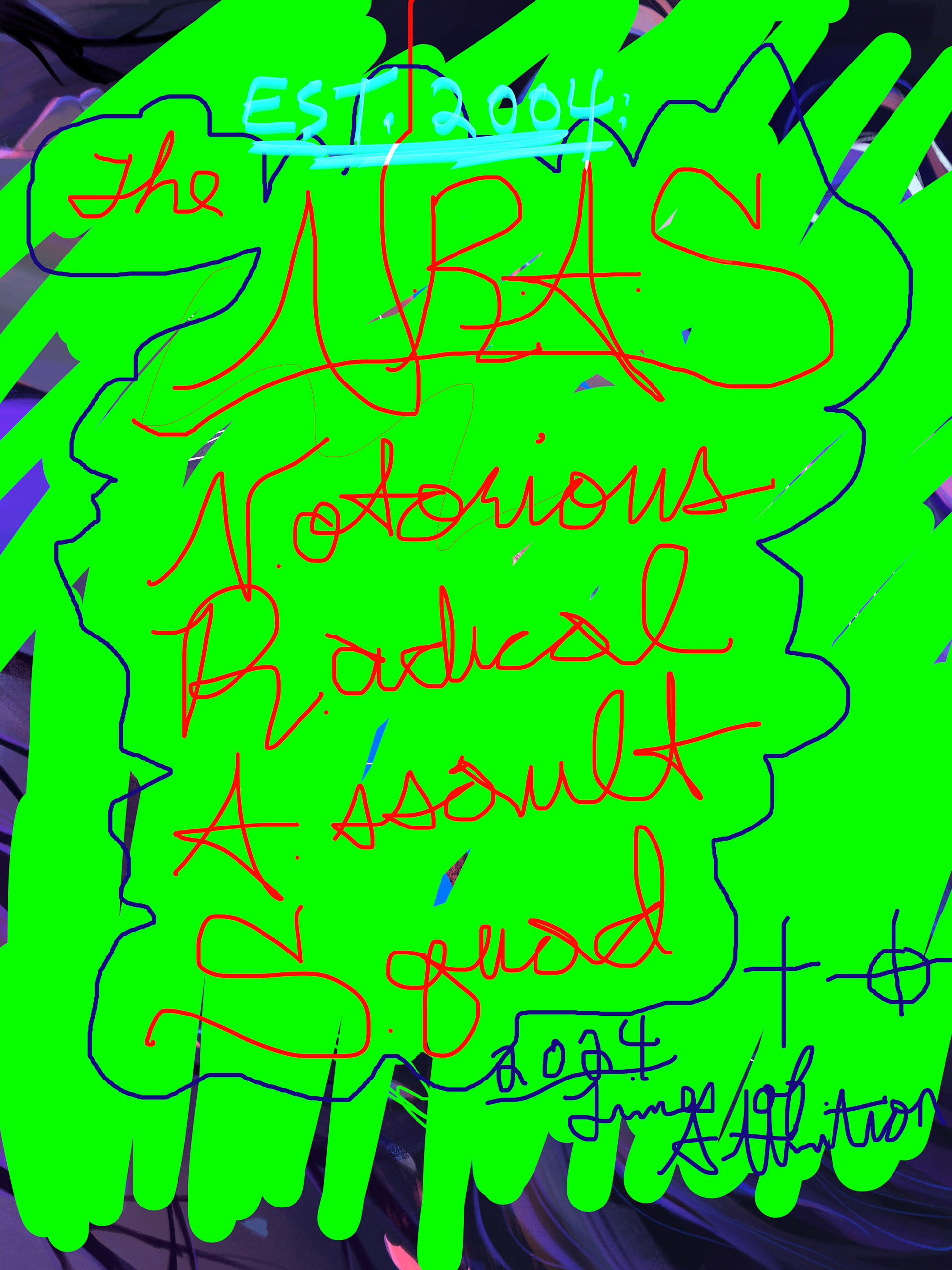

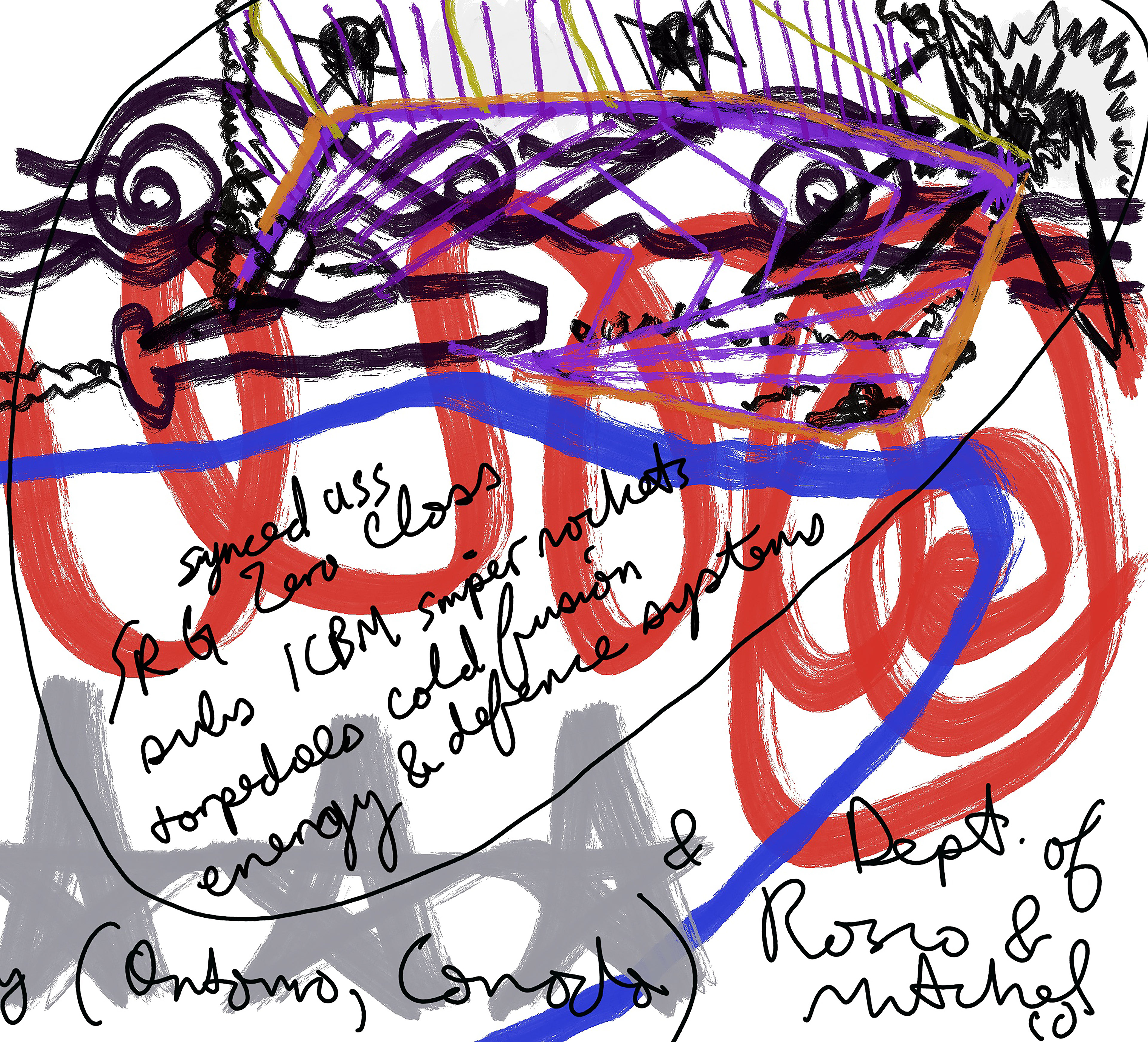
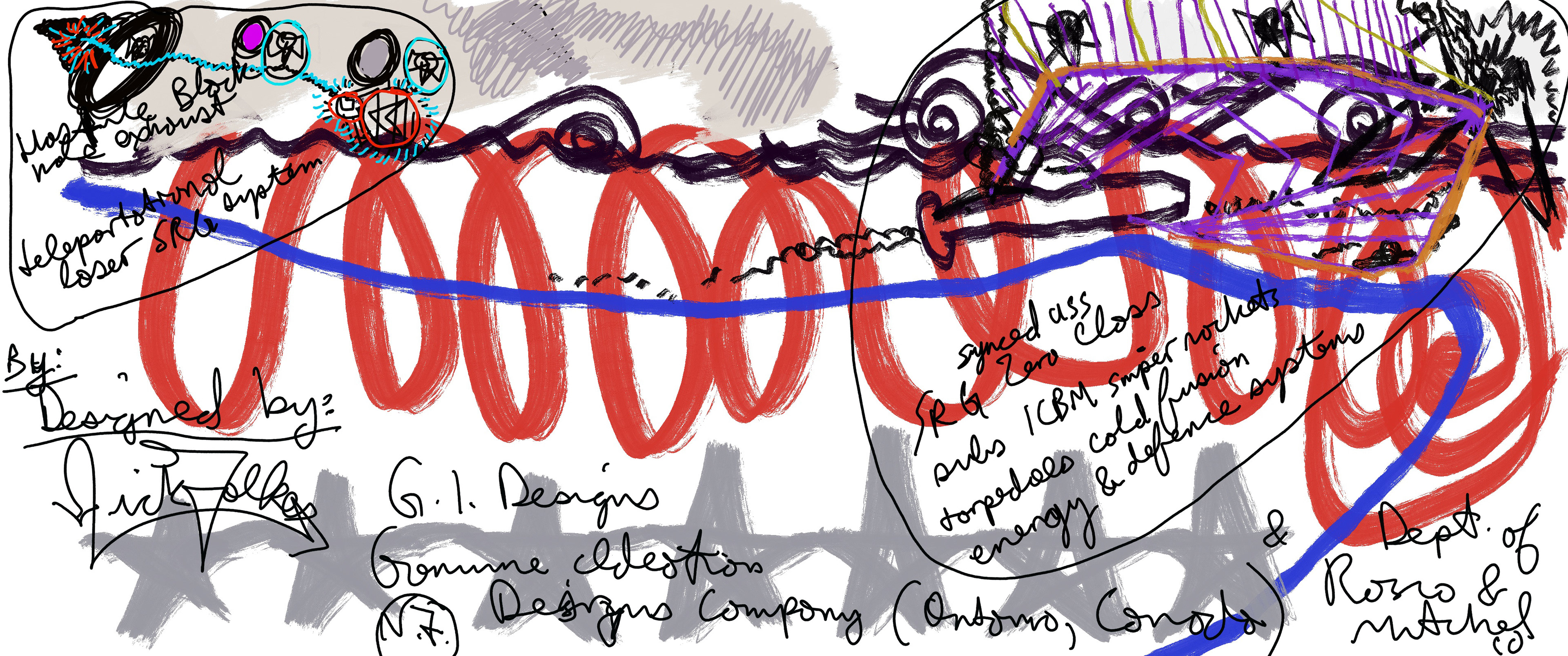
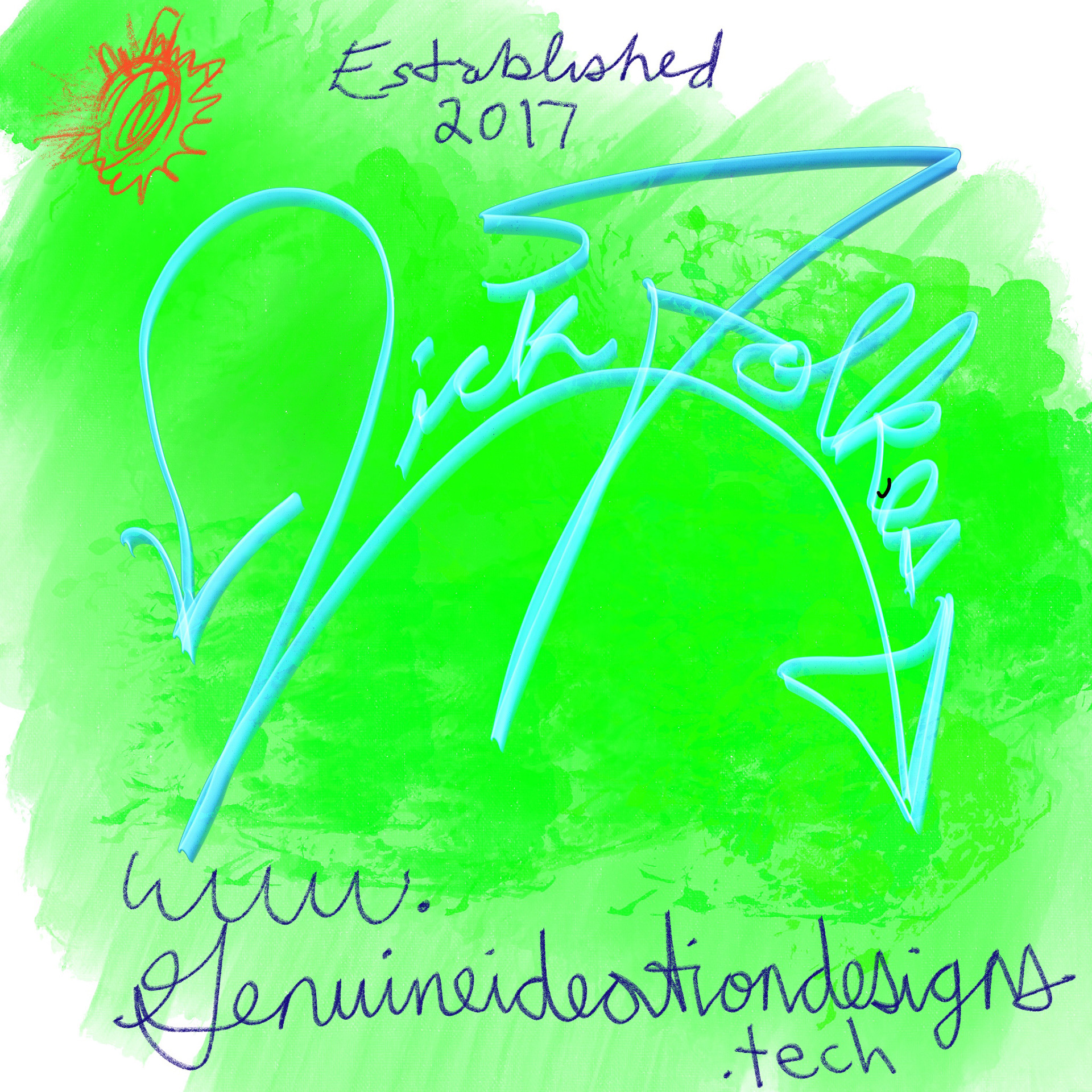